Automatic organic fertilizer granulation production line,the motor outputs through a belt and a reducer, and the gear drives the granulation disc, thereby driving the rotation of fertilizer raw materials. Under the action of neutral and centrifugal forces generated during the rotation process, small particles roll downwards towards the edge of the steering wheel and continuously adhere to the powder, gradually increasing in size. At the same time, due to the frictional force of the disc body of the disc granulator, the particles roll upwards with the disc. When they reach the position of the scraper plate, the fertilizer raw materials that have not yet formed particles pass through the gap between the scraper plate and the bottom of the disc, while most of the particles slide down along the scraper plate and adhere again during the rolling process at the edge of the disc. After multiple cycles, the particles grow from large to small, reach the strength of the finished product, and overflow from the edge of the disc.
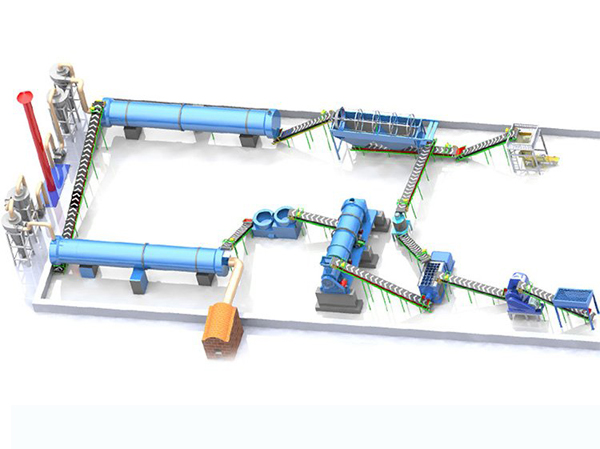
Automatic organic fertilizer granulation production line
processing capacity:1-100T/h
Application scope: variety of plant residues (crop stalks, weeds, leaves, peat, garbage and other waste, etc.) as the main raw materials, mixed with human and animal manure, composted and decomposed organic fertilizer.
Technical advantages of Automatic organic fertilizer granulation production line
- It has a good polarizing effect and can control the solution to spray on fine particles, resulting in a high balling rate and less production of large particles. All operations are intuitive, allowing for quick detection of operating conditions during the process, timely adjustment, and greater flexibility in producing various products with a wide range of force control.
- The granulation disc adopts an integral circular arc structure, with a success rate of over 93%.
- The reducer and motor are driven by flexible belts, which ensures smooth starting, reduces impact force, and improves equipment service life.
- The bottom of the granulation disc is reinforced with multiple radiating steel plates, which are sturdy, durable, and deformed.
- Thick and sturdy base design, no need for anchor bolts to fix, smooth operation.
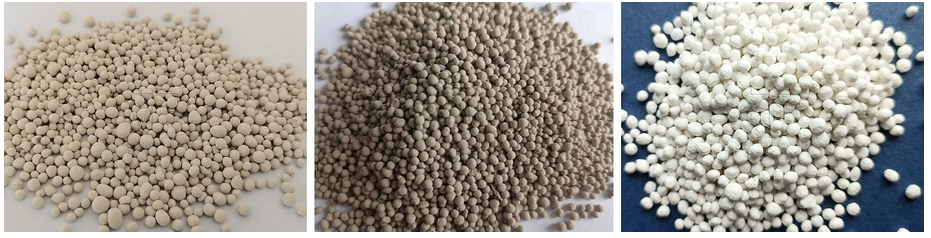
Wide adaptability of raw materials, can be used for compound fertilizer, medicine, chemical, feed, coal, metallurgy and other raw materials granulation, and can produce various concentrations, various types (including organic fertilizer, inorganic fertilizer, biological fertilizer, magnetic fertilizer, etc.) compound fertilizer.
Process flow of automatic organic fertilizer granulation production line
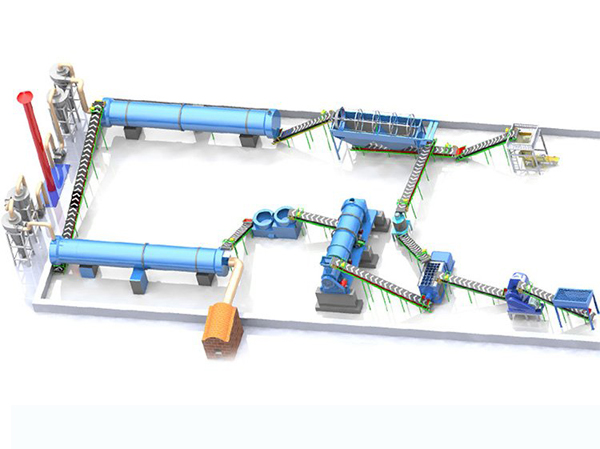
Process flow: batching system – drum screening machine – vertical mixer – drum granulator – dryer – cooling machine – automatic packaging machine.
Ingredient system
The automatic batching system mainly consists of a feeding system, weighing device, material bin, and conveyor belt. And the static batching system has both the speed of dynamic batching and the accuracy of ordinary static batching (0.2%). The PLZ automatic batching machine is mainly suitable for mixing, batching, and feeding 3-8 types of materials. The machine adopts a computer scale for automatic control, and uses a pneumatic door to control the quantitative feeding of the main material bin. After the materials are mixed in the mixing bin, they are automatically sent out by a belt conveyor. This machine has the advantages of simple operation, high ingredient accuracy, adjustable material ratio, energy saving, easy installation, and mobility.
rotary sieve
Drum screening machine is a commonly used equipment in organic fertilizer production, mainly used for the separation of finished products and return materials, and can also achieve the grading of finished products, making them evenly classified. Adopting a combination screen, it is easy to maintain and replace. The machine has a simple structure, easy operation, and smooth operation.
Vertical mixer
There are various forms of vertical mixers, and commonly used vertical mixers are mainly composed of: motor wheel, motor, barrel body, screw, discharge port, cleaning port, pulley, window, ladder, inlet, electrical box, circulating feeding port, feeding port, etc.
Rotary Drum Granulator
The rotary drum granulator has the characteristics of beautiful appearance, simple operation, low energy consumption, long service life, uniform drying, and easy maintenance. It is one of the more advanced granulation equipment in China. This product is suitable for cold and hot granulation as well as large-scale production of high, medium, and low concentration compound fertilizers. The product is now widely used in various places.
dryer
There are various types of organic fertilizer dryers, including chicken manure dryer, cow manure dryer, horse manure dryer, pig manure dryer, duck manure dryer, goose manure dryer, etc. The finished product of the organic fertilizer dryer has fine particles, and the dried product can be used as a culture medium for growing edible mushrooms such as Agaricus bisporus, or as feed for breeding turtles, fish, snails, chickens, ducks, etc.
Cooling machine
Cooling machines are used in organic fertilizer production to cool fertilizers at a certain temperature and particle size. When used in conjunction with drying machines, they can greatly improve cooling speed, reduce labor intensity, increase yield, further remove some moisture, and reduce the particle temperature of organic fertilizers. It can also be used for cooling other powdered and granular materials. The device has a compact structure, high cooling efficiency, reliable performance, and strong adaptability.
Automatic packaging machine
Automatic packaging machine is used for automatic quantitative packaging of powdered materials such as flour, starch, and feed in industries such as food, chemical, light industry, and building materials. The automatic packaging machine is designed with a reasonable structure and reliable performance. The automatic packaging machine adopts dual synchronous belt film pulling, controlled by a cylinder for tension, automatic correction, and automatic protection functions to minimize losses. The measuring device is matched and integrates bag making, filling, and other functions. The opening and closing method of the measuring device can be modified according to the material.
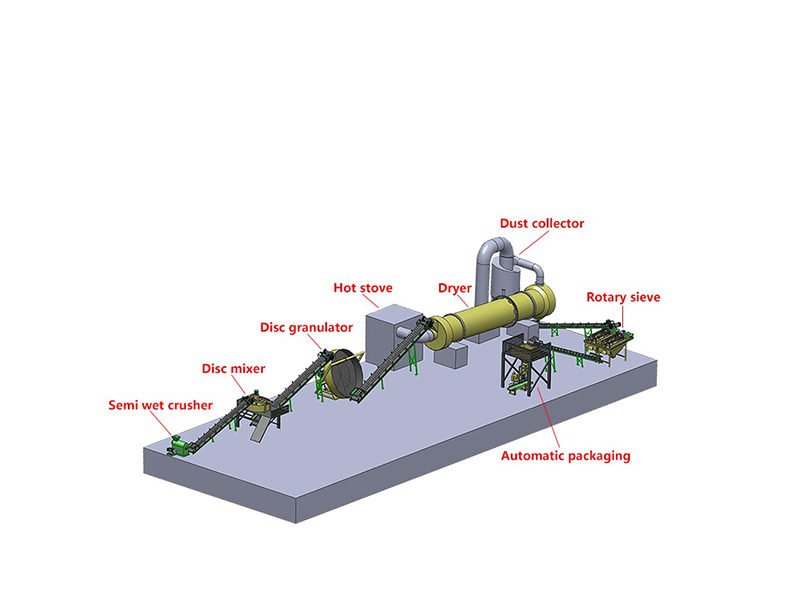
In terms of the material feeding amount of the disc granulator, it should be evenly fed and not suddenly fast or slow. Adjust the nozzle according to the principle of mechanics, under the same pressure, the nozzle has a smaller nozzle hole and a lower droplet density, while the nozzle hole has a larger nozzle hole and a higher droplet density. Strictly controlling the amount of water sprayed and adjusting the appropriate amount of water can effectively improve the ball formation rate and yield. Non powered or powered scraper assistance can also be installed. The size of the machine, the speed of the disc, and the inclination angle of the disc are also factors that affect the granulation effect.
Main equipment of drum disk granulator production line
Grinder | Mainly used for crushing raw materials to achieve granulation requirements |
Blender | Used for mixing and stirring materials, adjusting the moisture content of materials, and adding trace elements to meet the needs of granulation. |
Disc Pelletizer | Used for manufacturing spherical particles. |
Dryer | Mainly used for drying after granulation, allowing the particles to quickly reduce moisture at high temperatures, facilitating storage, and achieving continuous and uninterrupted production. |
Cooling machine | Mainly used for cooling and dehumidification after drying, to quickly reach room temperature of materials, meet storage requirements, and achieve continuous and uninterrupted production. |
Screening machine | Mainly used for separating finished products and returned materials, it can also achieve the classification of finished products, making them evenly classified. |
Coating machine | Mainly used for dust removal of granular powders or liquid coatings, it can prevent agglomeration and improve brightness. It can also be used for various multifunctional bacterial fertilizers. |
Automatic packaging machine | It mainly consists of the host, machine column, sewing machine head, conveyor belt and other parts. Can be packaged in different specifications to improve work efficiency and reduce operating costs. |