The liquid automatic batching system is an efficient and precise industrial automation equipment used to achieve accurate batching and mixing of liquid materials in manufacturing and production processes. This advanced technology aims to improve production efficiency, reduce labor costs, and ensure consistent quality of the final product.
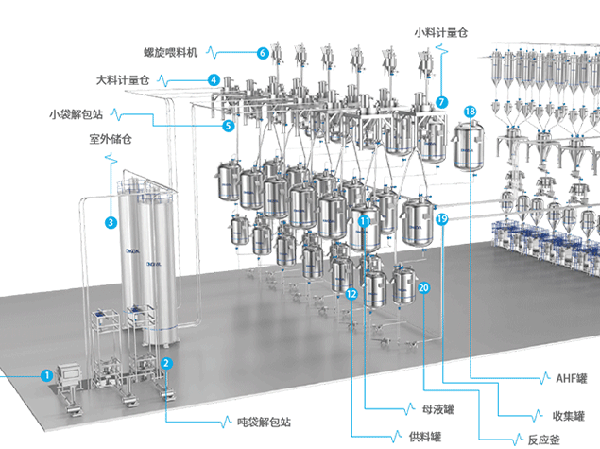
Automatic material liquid batching prodution plant system
Liquid automatic batching systems are widely used in various industries, including food processing, pharmaceuticals, chemicals, cosmetics, paints, coatings, etc. It can meet the precise ingredient and mixing needs of different industries, improving product consistency and quality. The liquid automatic batching system is a modern production tool that brings efficient, precise, and reliable batching and mixing solutions to various industries. By using liquid automatic batching systems, manufacturing companies can improve production efficiency, reduce costs, and ensure product quality and consistency.
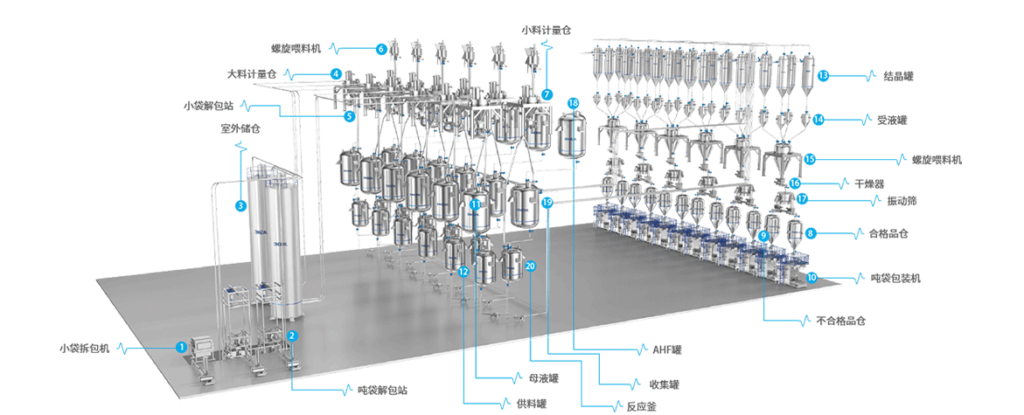
peculiarity | Positive pressure thin phase pneumatic conveying | Negative pressure thin phase pneumatic conveying | Positive compaction phase pneumatic conveying | Pneumatic nitrogen circulation |
---|---|---|---|---|
Application scenario | Scattered transport from one place to several places | No dust, deep or low material, Feed materials from multiple places to one place | Mass conveying, fragile particle conveying, Powder conveying | Potentially explosive, radioactive, Oxidizing material |
Environmental isolation effect | Positive pressure system to isolate dust and rain | Negative pressure environment, no dust | Positive pressure system, less material crushing, less wear | Safe isolation reduces the risk of dust explosion |
Operational stability | The flow pattern, speed and pressure are stable and reliable | Dust is not easy to spill | Suitable for fragile particles, simple separation and dust removal | Energy saving, nitrogen recycling |
Energy consumption | normal | low | low | Energy conservation |
Material handling performance | normal | No dust, suitable for materials with special requirements | Suitable for fragile materials, particle size less than 2mm | Suitable for hazardous materials |
Material handling application range
Profession | Materiel |
---|---|
Petroleum and chemical industry | PP, PE, petroleum coke, potassium sulfate, CaCO3, ABS, PVC, BaSO4, BPA, HDPE, CPE, EFP, EPC, EPVC, PVB, PA6, PC, PET, PVA, melamine, potassium bromide, sodium bromide, ion exchange resin, thiamine, polyacrylamide, urea, Plastic particles, TPU, SAP, lithium cobaltate, polystyrene, dry glue powder, compound fertilizer, adipic acid, divinegar tablets, monoamine phosphate, dicyandiamide, Polyformaldehyde, VD3 powder, etc |
Building materials | Silica black, activated carbon, bleached earth, calcined kaolin, silicon carbide powder, talc powder, silica sand, zeolite, slaked lime, rubber, quartz powder, carbon black, Cement, wood powder, wood chips, hard asphalt, perlite powder, talc powder, sanding powder, phosphogypsum, dry mix mortar, gypsum powder, dry sand, aluminate, Heavy calcium powder, graphite, zirconium aluminum beads, bauxite, white lime, clay, wood chips, carbon and so on |
Grain, oil and food | Wheat, soybean, corn, fructose, apricot stone (with shell), soybean meal, soybean skin, gluten, peanut, milk powder, soybean powder, rice husk, Starch, food grade Xanthan gum, threonine, corn germ, flour, yeast powder, feed granules, protein powder, bran, sesame, tapioca starch, Rice, pectin, peas, dehydrated garlic slices, lees, rice bran, peanut cake, MSG, cinnamon powder, coffee powder, maltodextrin, thirteen incense, etc |
Metallurgical minerals | Calcium carbide, silica powder, bentonite, limestone powder, alumina, zinc calcine, iron concentrate powder, potassium feldspar powder, cordierite powder, stone powder, calcium oxide, Titanium concentrate powder, bauxite powder, phosphate powder and so on |
Non-ferrous metal | Titanium dioxide, magnesium oxide, aluminum hydroxide, vanadium catalyst, titanium dioxide, aluminum oxide powder, potassium chloride, glauberite, magnesium hydroxide, antimony oxide powder, Copper powder, zirconium aluminum composite beads, aluminum fluoride, soda ash, etc |
medicine | Glucose, enzyme preparations, etc |
Chemical fiber | Alkali fibre |
coal | Coal coke, lignite, coke powder, pulverized coal, etc |
electricity | Fly ash, dust, soot, boiler slag, etc |
steel | Metal ash, kiln ash, sulfur iron slag, vanadium catalyst, etc |
Environmental protection energy | Calcium powder, calcium carbide slag, desulfurization ash, etc |
This liquid distribution and batching production line is widely used in the continuous production of large and medium-sized chemical enterprises. The batching only requires manual input of two or more materials into each storage tank, and the computer control system automatically adds various liquids according to pre-set proportions. The liquid is powered by a chemical pump and automatically added according to the proportion of each material using a high-precision flow meter; Continuous and uninterrupted production can be achieved by intermittently adding one or more materials based on time.
The liquid weighing system is suitable for the petroleum, chemical, and proportioning industries. The weighing system is based on computer technology, control technology, communication technology, and graphic display technology (i.e. 4C technology). The automatic weighing and batching system connects the on-site control station, control management station, detection station, and operation control center operation management station and engineer station distributed in the industrial site (nearby) through a communication network to jointly complete a comprehensive control system of decentralized control and centralized operation and management.
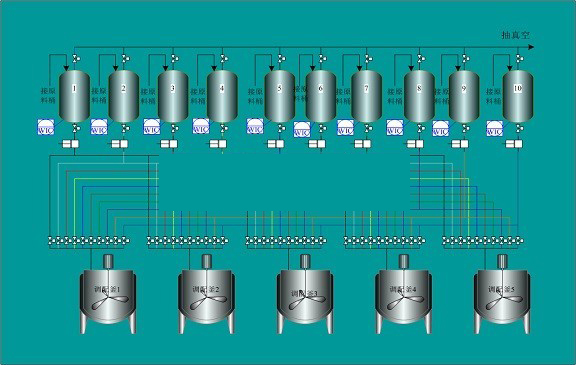
(1) High level tank weighing, measuring and batching
The materials are pumped from the tank area or intermediate tank, raw material bucket to the high-level weighing and measuring tank. Then, according to the formula requirements, the high-level weighing tank materials are sequentially or simultaneously placed into the mixing kettle, and the discharge valve is controlled according to the formula value to complete the automatic batching control of a batch
(2) Mixing kettle, weighing and measuring ingredients
Using a mixing kettle for weighing, a high-level tank is equipped with a liquid level indicator, and the discharge process controls the valve entering the mixing kettle. The feeding valve is controlled according to the weight changes of the mixing kettle. This batching mode can only be fed sequentially, not simultaneously, and the batching speed is slow.
(3) Bucket loading ingredients
The raw materials in barrels are sequentially drawn into the batching kettle according to the formula, and the batching kettle is weighed and measured. Manually insert the extraction tube, manually start the extraction program, and the computer completes the measurement and extraction control.