The chelation and complexation technology of biogas slurry, amino acid, humic acid, large number of elements and medium amount elements in liquid water soluble fertilizer production line has a set of strict operating process and systematic management methods. The use of water-soluble fertilizer equipment + professional technology produced by our company can improve the work efficiency considerably compared with the same industry products, and the quality of finished products is supported by a variety of production processes and formulas, which maintain a high level in the same industry.
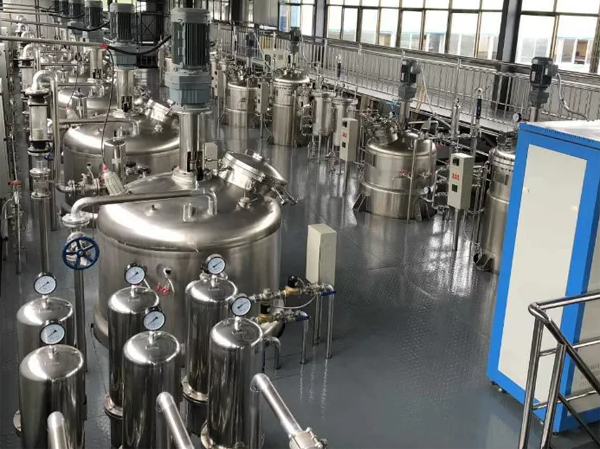
Automatic liquid water soluble fertilizer production line
processing capacity:1-100T/h
Production capacity: 1–100 tons/day (according to customer requirements, customized) Applicable materials: biogas slurry, livestock and poultry breeding enterprise wastewater, food processing and drug processing waste, amino acid leftovers, trace elements, etc. Application: biogas engineering, livestock and poultry breeding enterprises, paper enterprises, monosodium glutamate production enterprises, food processing plants, drug processing plants, etc.
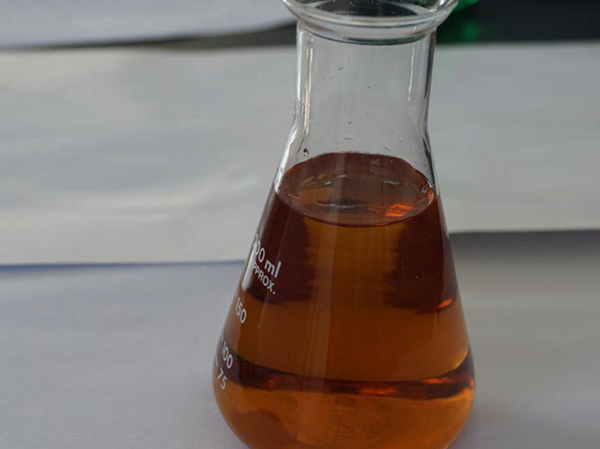
Water-soluble fertilizer is a new type of fertilizer that can be completely dissolved in water. The liquid water-soluble fertilizer has sufficient nutrients, uniform distribution and high organic matter content, which can activate soil, increase soil aggregate structure, retain water and fertilizer, and reduce the amount of fertilizer used in the planting process. The production process of liquid water-soluble fertilizer is almost the same as that of solid ordinary BB fertilizer, but the reflected changes in the nature of raw materials are essentially different.

Water soluble fertilizer production line process flow
- Stock liquid — sedimentation tank — (bacteria machine) — solid liquid separator — digester — finished product tank
- Raw water — suspension preparation — automatic dosing — element reaction tank — cooler — finished tank
Water soluble fertilizer production line performance characteristics:
- The process is simple and convenient, eliminating the process of water treatment and sedimentation of biogas slurry according to flocculation ultrafine filtration. The organic matter content and total nutrients of the marsh fertilizer were improved through the whole production process, and the organic matter content of the finished fertilizer exceeded the standard of ***Y1106-2010 (water soluble fertilizer containing humic acid).
- Water soluble fertilizer equipment, can produce NY-1107/NY-1428, soil conditioner and other fertilizer equipment variety, advanced technology.
- Use the residue of biogas, biogas residue and biogas slurry for biological breeding.
- The use of biological deodorization, and the addition of the formula developed by the Academy of Agricultural Sciences, combined with the bacteria breeding machine equipment, effectively adjust the five internal hormones in the filler, promote biological active enzymes, so that microorganisms quickly attached to the surface of the filler elements, can quickly absorb and degrade the foul ingredients in the biogas residue and biogas slurry, while maintaining the metabolism of microorganisms themselves, the effect is ideal.
- Bioleach and biogas slurry are pumped into the bacteriotrophic machine for deodorizing fermentation. At the same time, bioleach and biological adsorption are adopted. Through anaerobic and aerobic alternating fermentation, humic acid chelation and element complexation reaction are rich in organic matter, nitrogen, phosphorus, potassium, a variety of nutrient elements and rich amino acids, humic acid and peptides, beneficial bacteria are natural marsh fertilizer. The biogas slurry after complete treatment is pumped into the sedimentation tank.
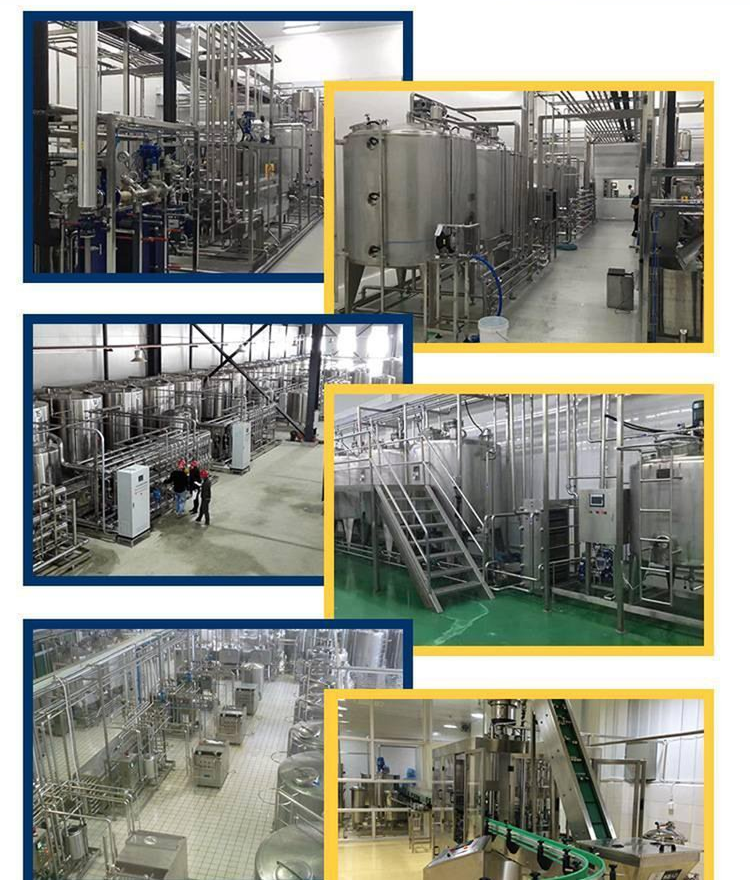
Main technical parameters of the complete production line for liquid water-soluble fertilizer:
- Filling range: 5-50L; 2. Measurement accuracy: ± 0.2% 3. Filling speed: ≥ 8 barrels/minute/four heads (20L)
The functions, processes, and equipment configuration of the complete production line for liquid water-soluble fertilizers are specified
- Process:
The climbing bucket elevator lifts the material into the reaction kettle, emulsifies and refines it through two filters, then filters it into an intermediate storage tank, fills it into a large bucket, seals it, and finally outputs the finished product.
- Equipment configuration: climbing bucket elevator, transition bucket and bracket, cubic reaction kettle, rotary pump and pipeline, emulsion pump, dual filter, cubic intermediate storage tank, large barrel filling line, and main control cabinet.
- Equipment introduction and requirements:
1) Reaction kettle
Specification 1000L, vertical, three-layer with mixing and insulation, material: The inner and outer pots are made of 304 stainless steel, the outer insulation board is made of stainless steel, and the insulation material is rock wool. Steel plate thickness: inner 5mm, jacket 4mm, foreskin 2mm;
Heating method: electric heating, with a total heating power of 56KW (controlled in four stages, with each stage having a power of 18kw)
Mixing device: motor power 5.5KW, 60r/min;
Import and export: one solid feeding port, three liquid feeding ports (with a reserved hole diameter of 50mm), and one discharge port;
2) Rotary pump
- Motor power: 5.5kw, flow rate:>10m3/h, outlet pressure 0.1-0.6mpa, all stainless steel structure. It can be linked with the level sensing switch of the metering high-level mixing tank to automatically control the start and stop of pumping work without manual intervention. This machine is suitable for automatic pumping of various fluids. High temperature resistance, no damage to pumped materials, smooth operation, and no noise; Easy to maintain.
- Power 5.5kw, flow rate>10m3/h, outlet pressure: 0.1-0.6mpa, all stainless steel structure.
3) Emulsification pump
Generate strong shear forces during high-speed rotation to achieve mixing, homogenization, dispersion, and crushing.
4) Joint filter
The sealing gasket is made of food grade temperature and oil resistant silicone rubber, and the filtration flux matches the entire production line. The filtration capacity is 10m3/hour and the filtration area is 0.3m2.
5) Weighing filling machine
① The weighing automatic filling machine consists of a linear arrangement of weighing platforms (with roller conveyors), a chain push rod in and out bottle mechanism, fast and slow filling (with cylinder diving) mechanisms, a feeding transition box, weighing control instruments, and programmable control units. The liquid filling scale can meet the needs of automatic filling of various liquids, and can meet the filling of liquid without foam and with foam.