Automatic organic and inorganic fertilizer production line is a kind of compound fertilizer machine containing both organic matter and fertilizer. It is a commercial fertilizer made from organic materials such as feces and peat, harmless and effective treatment by microbial fermentation, and adding an appropriate amount of fertilizer, humic acid, amino acids or beneficial microorganisms through granulation or direct mixing.
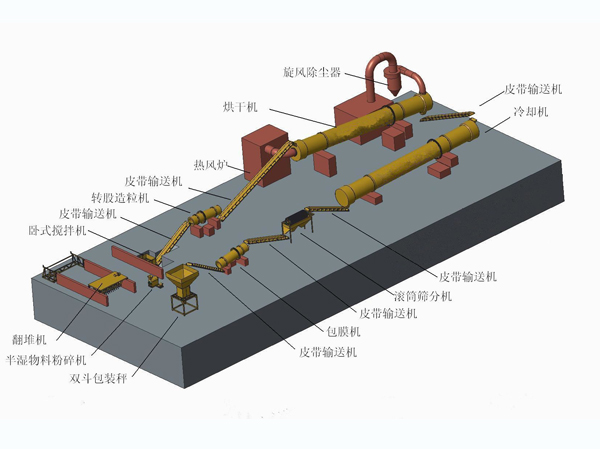
Automatic inorganic fertilizer production line
processing capacity:1-100T/h
Application scope: variety of plant residues (crop stalks, weeds, leaves, peat, garbage and other waste, etc.) as the main raw materials, mixed with human and animal manure, composted and decomposed organic fertilizer.
Establishing an organic manure production plant is a good choice for you to get profits. It can not only recycle your organic manure waste, but also bring you economic efficiency. While, it is important for you to know the details about being an organic manure fertilizer manufacturer. For example, you should know the process for turning your animal waste to available fertilizers. Meanwhile, there are many machines for processing your manure fertilizers efficiently and conveniently. Here we provide you the details about the processes, machines, required area and the cost. Besides, you can also get professional solutions and equipment for your own manure fertilizer making requirements at the best price.

The organic-inorganic compound fertilizer production line is a complete set of equipment for processing organic fertilizers using feces as raw materials. The feces from the feces pit can be pumped into the equipment through a mud pump using a feces treatment machine, and then dehydrated by the equipment. After treatment, the moisture content is about 40%. Alternatively, crops such as straw and rice bran can be used as fillers, and then biological bacterial agents can be sprinkled on them. 1KG of bacterial agents can be mixed with 20KG of water and transferred into the raw materials, which can ferment 1 ton of raw materials. 4. Flip and toss once every 5 days, and it usually takes 10-15 days to fully mature. The entire set of equipment requires fermentation turner, semi wet material crusher, drum screening machine, horizontal mixer, disc granulator, dryer, cooler, drum screening machine, coating machine, automatic quantitative packaging machine and other equipment
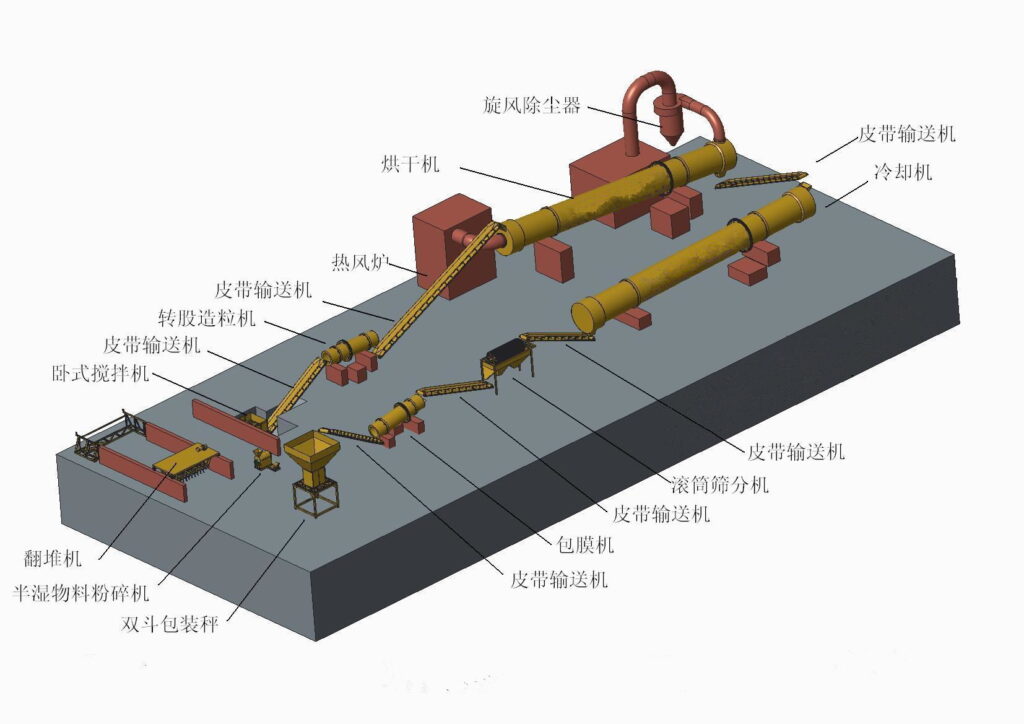
Fermentation turning machine – crusher – mixer – disc granulator – dryer – cooler – screening machine – packaging machine, connected by a belt conveyor in the middle. Different production volumes result in different product models.
1.Directly feed the recycled livestock and poultry manure into the fermentation area. After one fermentation and two aging stacking, the odor of livestock and poultry manure is removed. At this stage, fermentation strains can be added to decompose the coarse fibers, so that the particle size after crushing meets the particle size requirements of granulation production.
2.After crushing and screening, the material enters the mixing and stirring system. Before mixing and stirring, according to the formula, N, P, K, and other trace elements are added to the mixing and stirring system to start stirring and stir evenly to achieve a uniform fertilizer efficiency content of the fertilizer particles as a whole.
3.Transport the mixed materials into the granulation system (a rotary drum granulator or an extrusion granulator can be used).
4.Particle drying: Send the granules made by the granulator into the dryer to dry the moisture contained in the granules, increase their strength, and facilitate storage.
5.Particle cooling: The temperature of the dried fertilizer particles is too high, making them prone to clumping. After cooling, they are easy to store in bags and transport.
6.Particle classification: The cooled particles are classified, and those that do not meet the requirements are crushed by a crusher and returned to the granulation system for further granulation. Screen out qualified products.
7.Finished product coating: Coat qualified products with coating to increase the brightness and roundness of particles.
8.Finished product packaging: The finished particles are bagged by an automatic packaging machine and stored in the warehouse.
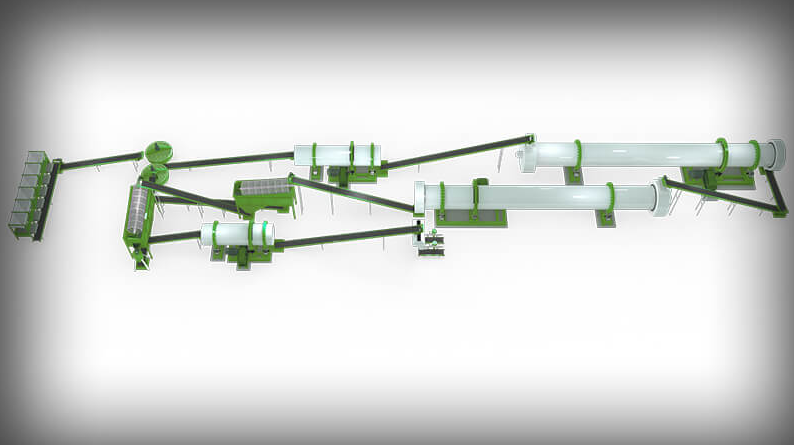
Overview of Organic Inorganic Fertilizer Production Line Products:
The disc granulator in the production line of organic-inorganic fertilizers adopts a circular arc structure for the granulation disc angle, with a yield rate of over 93%. The reducer and motor are driven by flexible belts, which ensures smooth start-up, reduces impact force, and improves the service life of the equipment;
The bottom of the granulation disc is reinforced with multiple radiating steel plates, which are sturdy and durable. The base design is not deformed, thickened, weighted, and sturdy, and does not require anchor bolts for fixation, ensuring smooth operation; The main gear of the disc granulator adopts high-frequency quenching, doubling its service life;
The surface and inner lining of the disc granulator are made of high-strength fiberglass, which is corrosion-resistant and durable This machine has the advantages of uniform granulation, high ball forming rate, smooth operation, sturdy and durable equipment, long service life, etc., and is highly praised by users. It is an ideal product chosen by a large number of users.
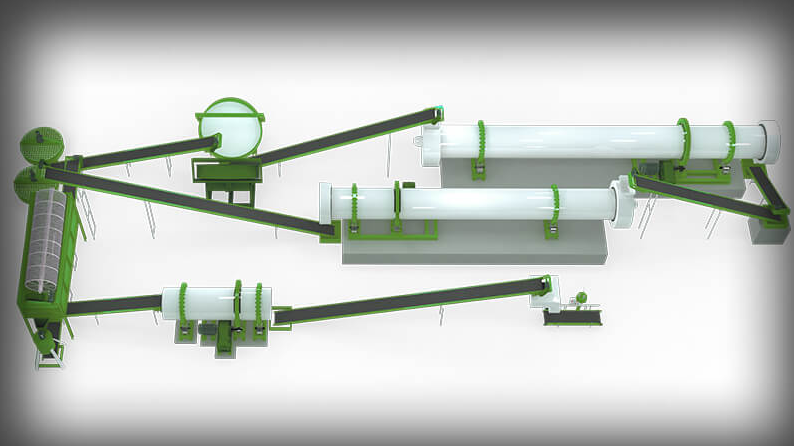
Working principle of organic-inorganic fertilizer production line:
The belt pulley and belt are driven by the main motor, and the small gear is transmitted through the reducer. The small gear meshes with the large gear fixed at the bottom of the disc to work towards the project; Through special and reasonable design, the big gear is installed on the main shaft fixed on the rack adjustment plate to support the work of the whole granulation plate (this machine is used together with the spray machine). After the materials enter the granulation plate, they are uniformly bonded together to form spherical particles through the continuous rotation of the granulation plate and the spray device; An automatic cleaning device is designed on the upper part of the granulation disc of the machine to prevent material from sticking to the wall, thereby greatly improving the service life of the machine.
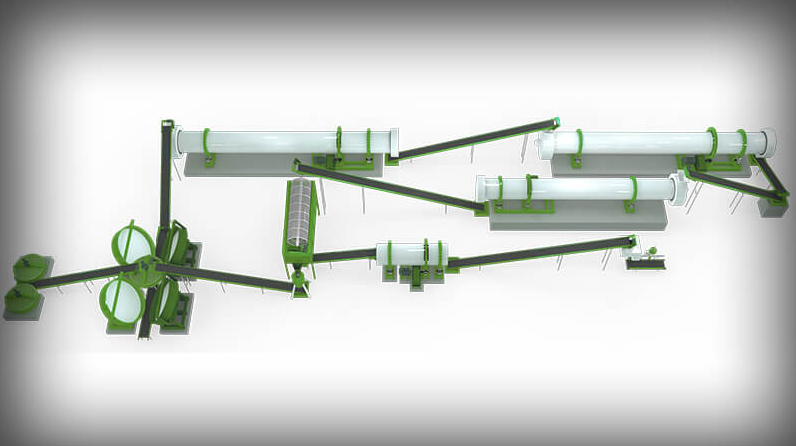
Application scope of organic-inorganic fertilizer production line:
The pellet products produced by the disc granulator are made from chicken manure, pig manure, cow manure, organic matter, urban waste, and sludge as raw materials. They can be customized into complete sets of production line equipment, such as chicken manure pellet production lines, pig manure pellet production lines, urban waste treatment production lines, and can produce 5 tons of pig manure or 10 tons of pig manure production lines at a time. They do not contain any chemical components because chickens and pigs have poor digestion ability and can only consume 25% of the nutrients. The other 75% of the nutrients in the feed are discharged with the feces, making the dry products rich in nitrogen, phosphorus, potassium, organic matter, amino acids, protein and other components. The organic fertilizer granulator has created economic benefits for enterprises and made significant contributions to human environmental protection engineering.
This machine has the characteristics of uniform granulation, high granulation rate, smooth operation, sturdy and durable equipment, and long service life, making it an ideal equipment for users to choose.

Advantages of Organic Inorganic Fertilizer Production Line Products:
- High ball formation rate, round and strong particles, intuitive operation, easy maintenance, etc.
- No drying process, room temperature granulation, one-time molding, low investment, fast results, good economic benefits.
- The power is small, the operation is reliable, there are no emissions of three wastes, the operation is stable, the maintenance is convenient, the process layout is reasonable, the technology is advanced, and the production cost is low.
- The raw materials have wide adaptability and can be used for granulation of various raw materials such as compound fertilizers, pharmaceuticals, chemicals, feed, coal, metallurgy, etc. It can also produce compound fertilizers of various concentrations and types (including organic fertilizers, inorganic fertilizers, biological fertilizers, magnetic fertilizers, etc.).
- Especially in the granulation of rare earth, ammonium bicarbonate, and ammonium sulfate compound fertilizers, it fills the domestic gap and ranks at the leading level in China. It is a promotion project for national environmental protection applicable technologies.