The automatic rotary tray production line is composed of a pulping system, forming system, drying system, stacking system, vacuum system, high pressure water system and and air compressor system. It is used to produce egg trays, fruit trays, etc. Using waste paper such as waste newspaper, carton paper, office paper, scrap and other waste materials as raw materials, it is prepared into a slurry with a certain concentration through hydraulic crushing, filtration, water injection and other processes, and is vacuumed on a special metal mold by a forming machine. It is absorbed into a wet billet, then dried by a drying line, and then stacked.
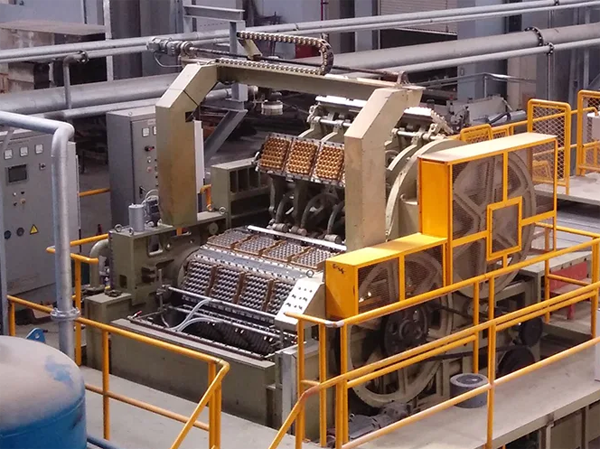
Automatic double rotary pulp moulding egg tray production line
Production line composition: Forming System:Forming System: 1drop/2drops/4drops rotary (with the function of washing mold / product burrs, equipped with preheating system).
Drying System: 6 layer drying line.
Stacking System: five channel stacker ;six channel stacker (with automatic counting function)
Forming platen size(mm): 1900×400 / 2250×400
Design capacity of production line(based on 30cell egg tray): 2200pcs/hour / 2700pcs/hour / 3600pcs/hour / 4300pcs/hour / 6000pcs/hour / 7200pcs/hour
Forming Type: Rotary drum suction molding
Forming cycle time: ≤ 20 plates/minute
Mold Distribution: 5pc/drop; 6pc/drop(basing on 30 cells egg tray)
Product height: ≤70mm
Heating fuels: Gas, Thermal oil, LPG, LNP or steam(if with steam, the drying system is to be lengthened basing on the specific output capacity)
Control method: PLC + touch screen

Double Rotary Egg Tray Machine is an ideal solution for large-scale egg tray production, offering high efficiency, increased capacity, and automation. It is suitable for businesses looking to scale up their production while maintaining high product quality. Suitable for the production of egg trays, fruit trays, drinking cup carrier trays, bottle trays and other regular shape standard products.
Egg tray raw materials: Waste paper boxes, waste books, waste newspapers, book scraps, recycled egg trays, and other waste paper materials.
Final products: 20 egg tray, 30 egg trays (including chicken egg, duck egg, goose egg, quail egg, etc.), 6 egg box, 10 egg boxes, 12 egg carton, 15 egg cartons, 18 egg box carton, fruit tray (apple tray, avocado tray, melon tray, mushroom tray), berry trays, coffee cup carriers, coffee cup holders, seeding tray, etc.
Technical Parameters of double rotary pulp moulding egg tray production line
Model | 7000B2C | 9000B2C | 12000B2C |
---|---|---|---|
Molding Machine | High Speed Double Rotary Technology | ||
Molding Faces | 6 Faces Forming + 6 Faces Transfer | ||
Platen Size | 850 × 460 mm | 1200 × 460 mm | 1600 × 460 mm |
Drops per Minute | 50-60 Drops | ||
Drying Oven | 10 Layers | ||
Drying Energy | Diesel / Natural Gas / LPG / LNG etc, or Boiler System of Steam / Conduction Oil | ||
Standard Capacity / Hr | 7,000 pcs | 9,000 pcs | 12,000 pcs |
Standard Capacity / Day | 168,000 pcs | 216,000 pcs | 288,000 pcs |
Floor Plan (m) | 72 × 18 × 8 m | 90 × 18 × 8 m | 90 × 24 × 8 m |
Labor / Shift | 5~6 | 5~6 | 6~7 |
Raw Material | Waste Paper | ||
Max Product Height | 70 mm |
Working Process of Double Rotary Egg Tray Machine

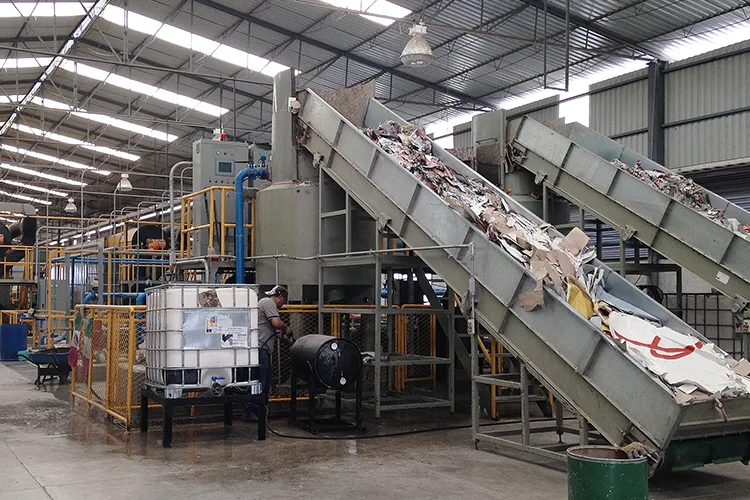
Pulping making system
The paper egg tray production line uses various types of waste paper, newspapers, magazines, corrugated cartons, etc., as raw materials. It is broken into fibrous slurry by injecting water into the hydraulic pulper. The broken slurry is vibrated to remove impurities and the sand is loosened and decomposed. The pulp, after impurity removal, enters the refiner for beating and refining. At this stage, additives and color pigments, etc., are added according to the customer’s needs, stirred evenly, and a slurry of appropriate concentration is prepared. This slurry is then transported to the slurry supply tank and awaits use by the molding machine in the next step. This step of the pulp molding pulping system is crucial to the formation and quality of egg trays.
Forming system
The forming system is a key process in the production of pulp molded egg trays. It plays a decisive role in the quality, breakage rate, production energy consumption, and production efficiency of paper-plastic egg trays. Below, we will use the Double Rotary Egg Tray Machine, which is extremely popular in the industry, as an example to explain:
The forming machine has various specifications such as 4 faces, 6 faces, 8 faces, and 12 faces, and is equipped with customized egg tray molds (egg cartons, fruit trays, cup holders, etc. molds can be replaced). It mainly operates using vacuum suction filtration technology. The prepared slurry in the slurry supply tank is transported to the molding machine. At this point, the molding machine starts to work. Through vacuum suction, the fibers in the pulp are evenly deposited on the surface of the forming die, and then extruded through the forming die and the transfer die to form a wet embryo of an egg tray. A large amount of moisture will be removed during vacuum suction, and the forming cycle generally ranges from 3 to 7 seconds. At this stage, the wet embryo has no hardness, but the basic prototype of the egg tray has been formed.
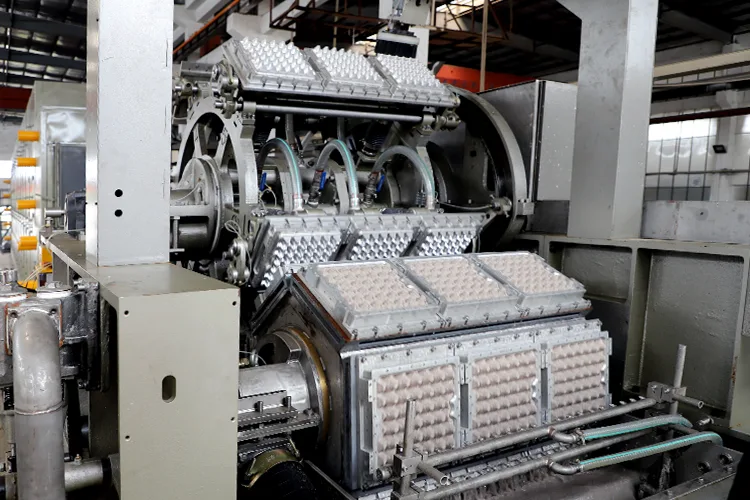
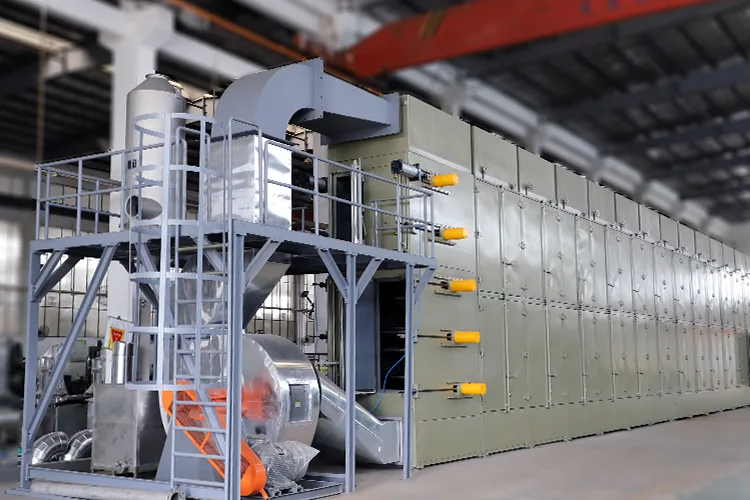
Drying system
After the egg tray forming is completed, the extruded egg tray wet embryo is transferred to the conveyor belt through the transfer mold. Then, the busy conveyor belt continuously carries the egg tray wet embryo into the drying system without stopping. The drying system can be heated by burning coal, wood, natural gas, or electricity. The dryer continuously emits heat and evaporates and dehydrates at high temperatures, reducing the moisture content of the paper mold egg tray to 10%~12% to achieve drying.
Which paper tray production equipment is better? Case sharing of zy6000 automatic egg tray line project in Saudi Arabia.
The production line adopts a fully automatic pulping system, the adjustment accuracy can reach 0.01%, the pulp concentration is stable, and the product quality is good.
The forming machine adopts 4-sided drum molding technology, with a production capacity of 6,000 pieces per hour, and the moisture content of wet blanks is low, about 69-70%, which saves 30% of energy consumption than other manufacturers.
The thermal efficiency of our multi-layer drying line is as high as 90%, with a small footprint, high efficiency and energy saving, and is equipped with a tail gas recovery and recycling system, which reduces the energy consumption by 24% compared with the traditional drying line.
The host system integrates forming, hot pressing, drying, conveying, and stacking. Each process is automatically and continuously completed to realize automatic operation. It is the best choice for the pulp molding industry to cope with the rising labor costs.