Degradable production line equipment with corn starch, pulp, rice starch, tapioca and other natural degradable materials as the main raw materials, through precision machining technology, the production of all kinds of degradable tableware, such as lunch boxes, cups, knives and forks, effectively replacing traditional plastic products, significantly reducing white pollution.
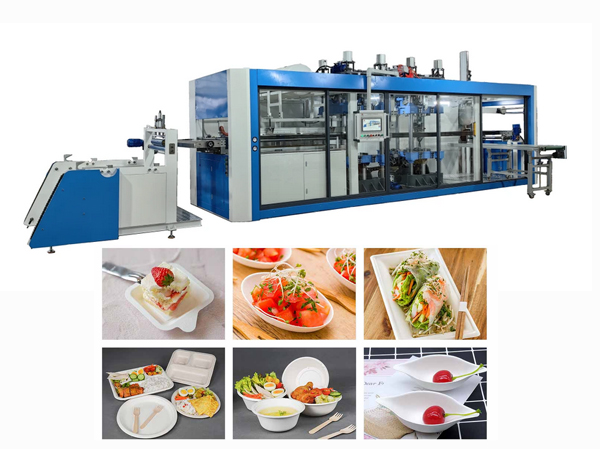
Automatic disposable degradable tableware production line
Automatic disposable degradable tableware production line,The biggest feature of the host system is that it integrates molding, hot pressing, cutting and stacking, which can be completed automatically and continuously without manual transfer, and can be realized online without removing molds and changing nets (5 minutes to complete). It greatly saves the space, labor and power consumption, improves the opening probability, product qualification rate and product quality, and is easy to maintain.
Product characteristics of disposable degradable tableware production line
- Energy saving
The transfer of products is achieved by using a motor-driven mesh frame, without the need for vacuum adsorption transfer, saving air pressure in the vacuum machine. - Save factory space
The single machine production capacity is 1T, with a single machine occupying an area of 22 square meters and a single machine production capacity of 49KG/day per square meter. - Fast mold installation, screen replacement, and long mold cleaning cycle
Complete mold installation within 2 hours; 5-minute non-stop network replacement; Clean the molds from January to March. - Good product quality
The mesh frame transfer mode ensures that the product has no process holes and no dirt or black spots. - Easy maintenance
The equipment adopts a pneumatic+servo drive system, and the product is transferred by the mesh frame. The hot pressing mold does not need to move horizontally, and there is no precision requirement for repeated positioning. It can be repaired and maintained by ordinary maintenance workers.
Serial number | project | Parameter index |
1 | Equipment name | Disposable tableware production line |
2 | model | WS-BYU043 |
3 | Template size | 1100 *800mm |
4 | Number of forming stations | 1 |
5 | Working mode of forming die | Vacuum slurry suction, vacuum dehydration molding |
6 | Number of hot press drying stations | 2 |
7 | Drying method | In mold drying and heating |
8 | Heating mode | Heat transfer oil heating |
9 | Heating power of heat transfer oil | If heat transfer oil is used for heating, the input requirement is 120000 kcal / h (Party A shall be responsible for the heat transfer boiler and pipeline) |
10 | Working pressure of hot pressing station | 40t (gas-liquid booster cylinder) |
11 | working temperature | Room temperature ~ 240 ℃ adjustable |
12 | Vacuum input requirements | -0.05—0.07MPa: Excluding manipulator:5-6m3/min Including manipulator:10-15m3/min |
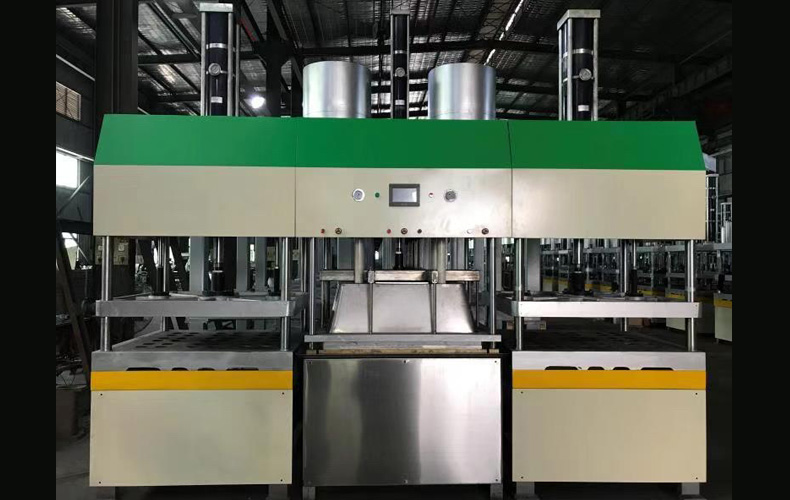
The design of the biodegradable tableware production machine is highly automated, from the mixing of raw materials, extrusion molding, drying and shaping to the final product packaging. The entire process adopts a PLC control system, which realizes functions such as parameter setting, data calculation, real-time monitoring, and fault alarm, greatly improving production efficiency and product quality.
Its unique inclined horizontal pressing structure and independent roller power design ensure the uniformity and dimensional accuracy of product layering, while also facilitating operation and maintenance.
In addition, these machines also have flexible and diverse production capabilities, which can quickly adjust production specifications and output according to market demand to meet the needs of different scenarios.
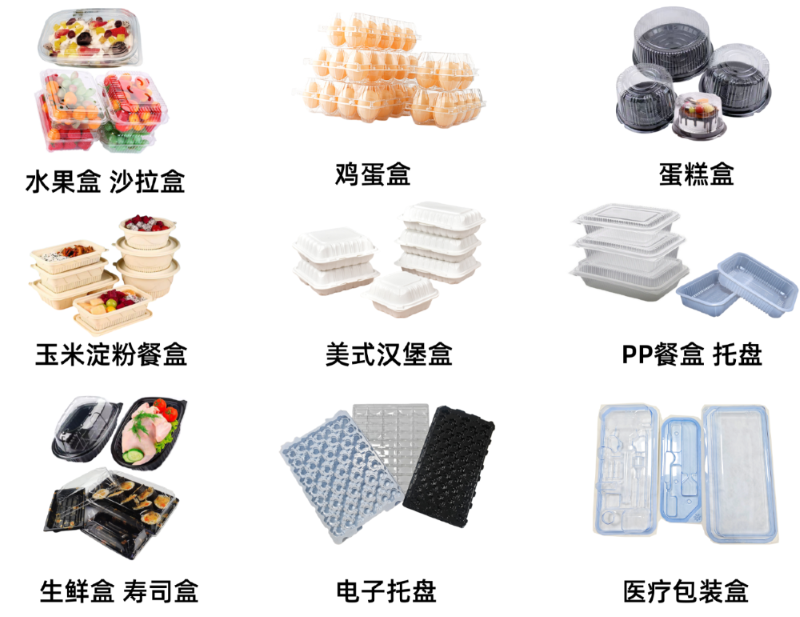
Degradable tableware production line main equipment
Machine features:
- Control system characteristics
(1) The human-machine interface adopts HD MCGS color iot touch screen, abnormal problems can be checked online, remote monitoring, troubleshooting, remote upgrade procedures, and problem solving;
(2) The machine system is the operating system developed by our company according to the existing national conditions, according to the operating habits of the boot master, the fastest number of empty machine test actions can reach 50 mode/minute, with the characteristics of complete functions, simple and easy to use, the master with the common machine foundation can learn 1-2 days to operate independently, and the master with other integrated machine experience can be familiar with operating the machine within 1 day;
(3) Monitoring and counting, station automatic lubrication, chain rail automatic lubrication, vacuum maintenance tips, but also can store documents, internal IO point monitoring and other functions
(4) The mold height data of the molding station is saved, the cutting position data is saved, and the beam width data is saved. During production, only the data saved for the first time is called to achieve rapid production, and the mold change machine speed is 20-30 minutes faster than that of peers.
(5) Other characteristics of the control system are detailed in the equipment manual;
- Loading area
2.2KW high-power motor is used for feeding, the diameter of the coil is up to 700mm, the maximum can be loaded 500KG/ supporting material, the feeding sheet is driven by rubber roller, there are two seamless steel pipe rods to replace the sheet, and the feeding sheet area is equipped with silicone oil injection device, which is convenient for stripping;
- Heat the area
(1) The electric furnace uses a specific aluminum furnace design, no deformation at high temperature, heat insulation cotton is added to the back of the heating brick electric furnace, and the heating wire is more durable;
(2) The heating brick uses Sweden Cornell heating wire, heating fast, good constant temperature effect, long service life and other characteristics, 5 years of ultra-long warranty, high temperature line using 2.5mm² (some peers are 1.5mm²), to ensure that the wire is durable and not easy to age;
(3) Temperature control module: the use of the latest temperature control module, temperature control is accurate, easier to adjust the temperature to do goods;
(4) The upper electric furnace dislocation adjustment function, baking sheet width less than 620mm can close a row of heating bricks, energy saving;
- Molding area:
(1) The molding length is 610mm, the width is 730mm, the upper and lower furnace is heated in three sections, and the molding height is up to 120mm;
(2) Both upper and lower molds use high-power servo motors to ensure that the machine can operate continuously for 24 hours;
(3) Water valve: the mold can only be watered under the automatic state to prevent mold condensation during shutdown and debugging;
(4) High memory of molding mold: call the mold high and low data saved in the first production, no need to adjust the mold, can be directly loaded mold production, improve production efficiency;
- Cut the area
(1) Cutting size 630×730mm, cutting die are equipped with heating knife electronic control system;
(2) Cutting position data preservation of the tool die: adjust the cutting depth of the tool die digitally, adjust the tool more accurately, do not damage the tool, can save the tool die position data, the second production, directly call the first production tool module data, can directly install the tool die production, reduce the waste of tool adjustment products, improve production efficiency;
(3) The upper and lower die adopts high-power servo to ensure that the cutting is powerful, and the cutting of various thickness materials is easy to cope with;
- Robot system
(1) The manipulator is stacked up and down with high-power torque servo to ensure that the machine can operate continuously for 24 hours;
(2) Manipulator mode: upper and lower stack, in-mold grab stack (customized), out-mold grab stack (customized);
(3) Discharge mode: side out or straight out (need to be determined) dual-use, so that the machine can adapt to all kinds of sites;
- Receiving system
(1) The receiving system uses torque reducer, simple adjustment, strong winding, and the traditional variable frequency motor control easy to burn motor;
- Chain rail transmission system
(1) The drawing servo adopts high-power servo to ensure that the machine can easily pull the 2.0mm thickness of the sheet;
(2) Automatic rail change function: just input the width data of the mold, the beam automatically adjusts the width, the beam width data can be saved, the later production, the beam data is directly called, and the efficiency of the transfer machine is improved;
(3) The use of high-precision reducer and spline shaft as the drive shaft, drawing precision;
(4) The chain rail adopts a hard oxidized girder with guide beads, and the hardness reaches 85° to ensure the durability of the girder;
(5) The chain adopts imported Donghua guide bead chain, which is not explosive edge, hardening and hardening, stable and wear-resistant;
- Cooling system
(1) 10P high pressure pump chiller, cooling effect is better, do goods faster;
- Vacuum system
(2) The use of 200m³/H vacuum pump, vacuum tank using large tank design, to meet the instant vacuum release, product molding quality is better;
- Lubrication system
(1) Station lubrication pump: with high pressure lubrication pump, 00# grease can be easily lubricated to each joint of the station to prevent station failure;
(2) Chain lubrication system: food grade 300 degree high temperature chain oil is used, and the chain guide rail is lubricated at the same time to reduce wear;