Automatic degradable pulp molded tableware production line is composed of a pulping system, forming equipment, vacuum system, high pressure water system and an air compressor system, and is used to produce disposable pulp molded tableware. The production line uses pulp from sugarcane, bamboo, wood, reeds, straw and other pulp boards as raw materials. The materials are prepared into a pulp with a certain concentration through the processes of hydra pulping, refining, adding chemical additives, etc. They are evenly attached to a special metal mold to form a wet blank product. A disposable pulp molded tableware product is produced through the processes of drying, hot pressing, trimming, and stacking. The average unit capacity of the forming system is 1T / day. And It can be customized per the actual order from the customer.
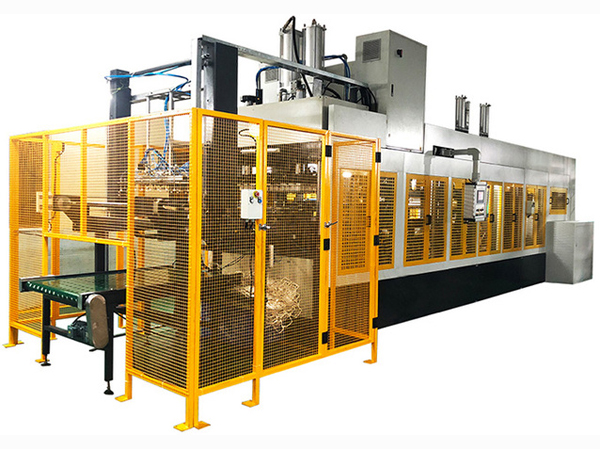
Automatic degradable pulp molded tableware production line
The biggest feature of the host system is the integration with forming, hot pressing, trimming and stacking. It is automatically and continuously completed without manual transfer, and can be achieved through the line without removing the mold and changing the mesh(completed in 5 minutes). This greatly saves the site, labor and power consumption, and improves the start-up rate, product qualification rate and product quality and provides easy maintenance.
At present, the paper pulp molding products are mainly environmentally friendly food packaging containers – meal bags, work bags, environmental food packaging containers mainly include paper pulp molding tableware, lunch boxes, convenient noodle bowls, plates, cups, plates, fresh dishes and so on; Pulp molding industrial packaging products mainly include shock-proof internal packaging of industrial products such as electronic products, medical instruments, gifts, etc. In recent years, these pulp molding industry packaging products have become more and more sophisticated and refined.
Degradable pulp molding products are made of annual herb fiber pulp (bagasse, reed, wheat straw, bamboo, etc.) as raw materials, adding additives, after special treatment, heating and pressing on the mold.
The pulp molded tableware production line is composed of a pulping system, forming equipment, vacuum system, high pressure water system and an air compressor system, and is used to produce disposable pulp molded tableware. The production line uses pulp from sugarcane, bamboo, wood, reeds, straw and other pulp boards as raw materials. The materials are prepared into a pulp with a certain concentration through the processes of hydra pulping, refining, adding chemical additives, etc. They are evenly attached to a special metal mold to form a wet blank product. A disposable pulp molded tableware product is produced through the processes of drying, hot pressing, trimming, and stacking. The average unit capacity of the forming system is 1T / day. And It can be customized per the actual order from the customer.
The biggest feature of the host system is the integration with forming, hot pressing, trimming and stacking. It is automatically and continuously completed without manual transfer, and can be achieved through the line without removing the mold and changing the mesh(completed in 5 minutes). This greatly saves the site, labor and power consumption, and improves the start-up rate, product qualification rate and product quality and provides easy maintenance.
The specific parameters of automatic degradable pulp molded tableware production line
Models | TSA3-11580 |
Equipment Composition | Forming,3 Phase Hot Pressing, Trimming, Stacking |
Platen Size | 1150mm*800mm |
Capacity Each Machine | 1Ton/day(basing on 9 inch round dish, 17g) |
Outline Dimension(mm) | L 13000 * W 3230 * H 3850mm |
Forming Type | Reciprocating pulp suction and forming |
The forming minimum shut height is 130mm. (mm) | 120 |
Hot-press standard mold closing height(mm) | 140 |
Forming Pressure | 5T |
Hot Pressing pressure | 40T |
Trimming Pressure | 60T |
Product Height(mm) | ≤65 |
Production Agle(度) | ≥10 |
Product transfer method | Servo drive chain drives mesh frame transfer products |
Heating Method Electricity | Electricity or Thermal Oil + Electricity |
Control method | PLC + touch screen |
Remarks | The above parameters are for reference. Due to the continuous development of technology, relevant data will be continuously updated |

The following data is the reference configuration of the production line, and can be customized according to the specific needs of customers.
Models | Output Capacity | Floor | Staff | Electricity | Water |
TWB4000 | 4Tons/day | 24 * 88Meters, height ≥5M | 5Persons/shift | 1000-1050KW/hour | 0.4-0.6Tons/hour |
TWB8000 | 8Tons/day | 24 * 120Meters, height ≥5M | 9Persons/shift | 1900-1950KW/hour | 0.9-1.1Tons/hour |
TWB10000 | 10Tons/day | 24 * 144Meters, height ≥5M | 11Persons/shift | 2300- -2400KW/hour | 1-1.3Tons/hour |
TWB20000 | 20Tons/day | 36 * 184Meters, height ≥5M | 22Persons/shift | 4500-4600KW/hour | 2.4-2.6 Tons/hour |
TWB30000 | 30Tons/day | 40 * 224Meters, height ≥5M | 33Persons/shift | 7000-7100KW/hour | 7-3.9Tons/hour |
TWB40000 | 40Tons/day | 40 * 264Meters, height ≥5M | 44Persons/shift | 9035-9450KW/hour | 4.9-5.1Tons/hour |
TWB50000 | 50Tons/day | 264 * 52Meters, height ≥5M | 54Persons/shift | 11400-11500KW/hour | 6.2-6.4Tons/hour |

- Energy-saving
The product transferring uses the motor to drive the mesh frame without vacuum adsorption transfer, saving the air pressure of the vacuum machine.
- Workshop space saving
Capacity Each Machine 1Ton, covering 22 square meters, and that is 49kg/square meter/day/machine
- Quick mold installation, mesh change, and long mold cleaning cycle
It takes 2 hours to complete the mold installation; 5 minutes without stopping to change the mesh; 1-3 Month cleaning the mold.
- Good Quality of Products
The mesh frame transfer mode makes the product free of process holes and dirt and black spots.
- Easy Maintenance
The equipment adopts a pneumatic + servo drive system. The product is driven by the mesh frame. The hot press mold do not need horizontal movement and no accuracy requirements of repeating positioning . The maintenance can be completed by ordinary maintenance workers.
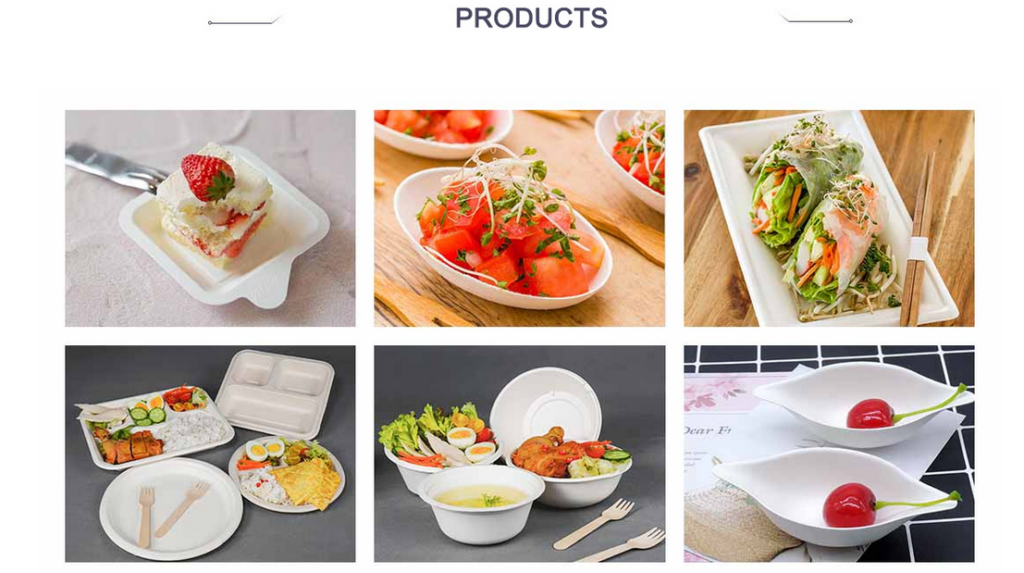

The unique performance advantages of pulp molding products:
(1) Pulp molding products are environmentally friendly and can be naturally degraded, and the pulp molding products buried in the soil can be completely naturally degraded within 3 months under the action of microorganisms, without centralized composting treatment. Plant fiber (pulp) molding products can be naturally degraded and recycled, is an environmentally friendly product.
(2) The pulp moulded products stored indoors can be placed for a long time (usually 10 years) before use without aging and deterioration.
(3) Pulp molded tableware products have a certain strength, good texture, smooth appearance; Pulp molding boutique industrial packaging products more exquisite appearance.
(4) Automatic pulp molding equipment production line has a strong versatility, replace the mold can be replaced by product types.
(5) Pulp molding products have good waterproof and oil-proof properties. In the manufacturing process of pulp molding products, adding appropriate amount of additives can produce waterproof and oil-proof effects.
(6) Wide source of raw materials, low cost. It is mainly annual herb fiber pulp or waste paper as raw materials, can be adapted to local conditions, local materials, inexhaustible.
The pulp mill can use wet raw pulp (bleached pulp or native color paste) as raw material for direct production; Other pulp molding plants can use commercial pulp for production.
(7) Less water consumption in the production process, no waste water discharge, in line with the requirements of clean production.
(8) Pulp molding products have good air permeability, and have unique benefits for the packaging of fresh products.
(9) Pulp molded products for fine industrial packaging have good seismic and buffer effects, and can effectively protect products from damage during transportation.
(10) According to the different requirements of users, the surface quality, color, graphics and other appearance elements of the product can be processed after processing.
(11) Low recycling cost, can be used repeatedly.
(12) Modern production technology can achieve high-speed, automated mass production.