The process flow of automatic compound fertilizer production line can usually be divided into: raw material ingredients, raw material mixing, raw material granulation, particle drying, particle cooling, particle grading, finished product coating, and final finished product packaging.
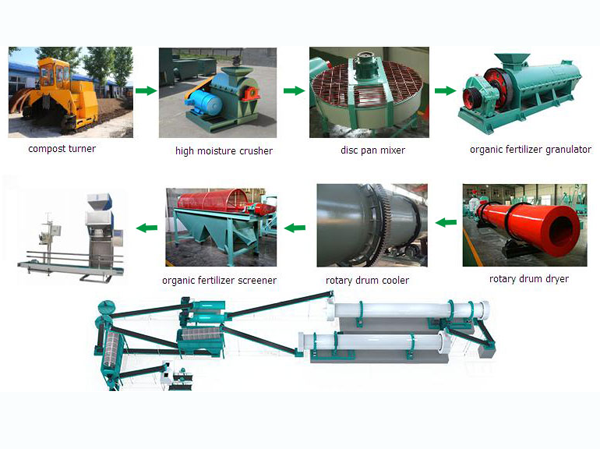
Automatic compound fertilizer production line
processing capacity:1-100T/h
Application scope: variety of plant residues (crop stalks, weeds, leaves, peat, garbage and other waste, etc.) as the main raw materials, mixed with human and animal manure, composted and decomposed organic fertilizer.
The equipment has the advantages of less investment, quick effect and good economic benefit. Complete equipment flow layout is compact, scientific and reasonable, advanced technology. Energy saving, no waste discharge, stable operation, reliable operation and easy maintenance. Wide adaptability of raw materials, suitable for compound fertilizer, medicine, chemical, feed and other raw materials granulation, product granulation rate is high. Can produce a variety of concentrations, a variety of types (including organic fertilizer, inorganic fertilizer, biological fertilizer, magnetic fertilizer, etc.) compound fertilizer. The company produces and sells products: no dry compound fertilizer production line, no dry compound fertilizer production machine, complete sets of compound fertilizer equipment, compound fertilizer equipment manufacturers, high tower compound fertilizer equipment.

The core technology of fully automatic compound fertilizer production line
(1) Tube reactor technology
Tube reactor technology, including hardware and process software packages. This technology has significant advantages in product quality compared to the traditional neutralization reaction tank+ammonification granulation process. Its characteristics are:
Advanced granulation technology
According to the nutrient requirements of compound fertilizer products, various liquid and solid raw materials measured by microcomputer batching are chemically reacted in granulators and tubular reactors to synthesize compound fertilizers, which are continuously wrapped in ammonia granulators to obtain completely spherical particles. The various nutrient ratios can meet the standards and are stable and guaranteed.
Product particle nutrient balance
Due to the chemical synthesis granulation, the nutrient content of granular fertilizers is the same as the labeling, and they can provide nitrogen, phosphorus, potassium, and other nutrients to crops in a certain proportion, ensuring balanced growth of crops.
The product has good physical properties and uniform particle size distribution, with 90% of particles having a diameter of 2-4 mm; High particle strength, good fluidity, and not easily broken during transportation, storage, and stacking.
(2) Melting urine granulation technology
The device adopts molten urine granulation technology, which can meet the requirements of producing various high nitrogen nutrient compound fertilizers on the one hand; On the other hand, it can further improve the quality of granulation, making the nitrogen nutrients of fertilizer particles more balanced, with a smooth surface and high glossiness.
(3) DCS control technology
According to the production characteristics of this device, phosphoric acid and NPK control rooms will be set up, using a distributed control system (DCS). Centralize monitoring and control of grinding, phosphoric acid, sulfuric acid/phosphoric acid tank area, NPK and other equipment through dynamic images throughout the entire process. The CRT in the control room can display various process parameters and the operating status of pumps; Automatic control of important process parameters can be achieved by starting and stopping the main pumps in the control room; By utilizing the powerful functions of DCS, it is possible to print production reports of various specifications on a scheduled or timely basis; Can display parameter violations, production accidents, or system failures in a timely manner; Capable of storing and displaying historical trends, and providing rich operational guidance information; Easy to operate and maintain
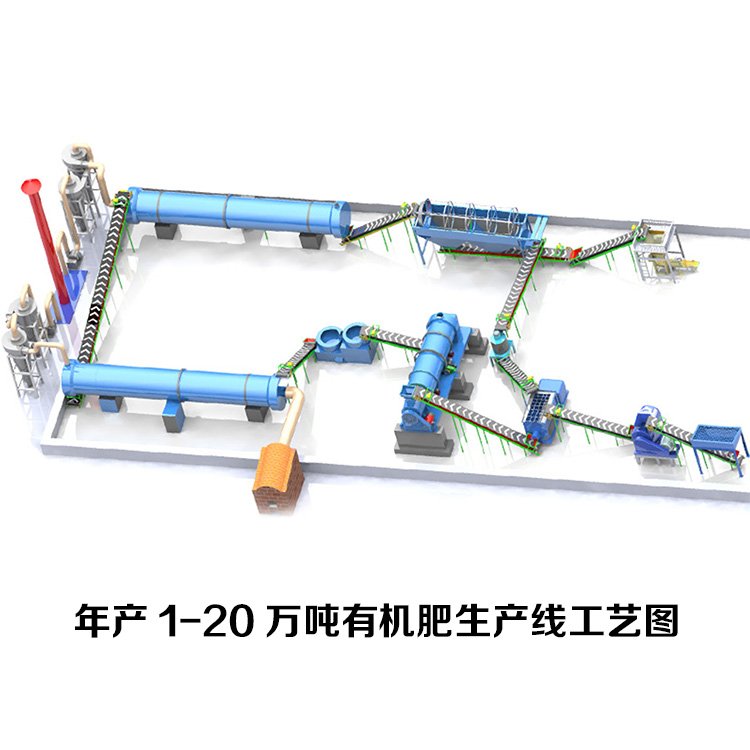
Raw material ingredients: urea, ammonium nitrate, ammonium chloride, ammonium sulfate, ammonium phosphate (monoammonium phosphate, diammonium phosphate, dicalcium phosphate, tricalcium sulfate), potassium chloride (potassium sulfate) and other raw materials are prepared in a certain proportion (based on market demand and soil testing results in various regions).
Raw material mixing: Mix the prepared raw materials evenly to increase the overall uniform fertilizer content of the fertilizer particles.
Raw material granulation: Send the mixed raw materials into a granulator for granulation (a rotary drum granulator or an extrusion granulator can be used).
Particle drying: Send the particles made by the granulator into the dryer to dry the moisture contained in the particles, increase their strength, and facilitate storage.
Particle cooling: The temperature of the dried fertilizer particles is too high, making them prone to clumping. After cooling, they are easy to store in bags and transport.
Particle grading: Classify the cooled particles, grind and re pelletize the unqualified particles, and sieve out the qualified products.
Finished film: Coating qualified products with film to increase the brightness and roundness of particles.
Finished product packaging: Pack the particles that have been coated with film, that is, the finished product, into bags and store them in a well ventilated area.
Project conditions: Taking the equipment configuration of a fully automatic compound fertilizer production line with an annual output of 10000 tons as an example (2-3 tons per hour)
Main raw materials: compound fertilizer materials such as nitrogen, phosphorus, potassium, etc.
Production capacity: 2 to 3 tons/hour per hour.
Factory personnel: produce approximately 900-1200 square meters; Approximately 5-8 people.
Equipment | Model number | Power (kw) | Quantity | Equipment use |
---|---|---|---|---|
Automatic batching system | ZD-N | 1.1 x N | 1 | Automatic computer proportioning system. (N indicates the quantity of raw materials) |
Double shaft mixer | TC-40 | 15 | 1 | Stir raw materials and adjust granulation water |
Rotary drum granulator | ZG-1.2 | 5.5 | 1 | The main granulation equipment, processing powdery materials into round particles. |
Disk granulator | YP-2 | 5.5 | 1 | Used for secondary granulation and particle shaping after drum granulation. |
Tumble dryer | HG – 1.2 | 7.5 | 1 | The finished particles are dried so that the moisture meets the storage requirements. |
Roller cooler | LQ – 1.0 | 5.5 | 1 | Cool the dried finished product particles to the appropriate temperature to prevent the finished product packaging from returning to moisture. |
Drum screen | GT – 1.2 * 4 | 5.5 | 1 | Finished particle sieving |
Roller cooler | LQ – 1.0 | 5.5 | 1 | Cool the dried finished product particles to the appropriate temperature to prevent the finished product packaging from returning to moisture. |
Drum screen | GT – 1.2 * 4 | 5.5 | 1 | Finished particle sieving |
Laminating machine | BM-1 | 4 | 1 | Used for coating finished particles, preventing caking and other functions. (Can be selected according to the demand of the production line) |
Packaging machine | Type 50 | Main motor 2.2 (Users need to be equipped with small air compressor) | 1 | Packaged finished products, ranging from 20kg to 50kg/ bag |
Belt conveyor | B500 | Equipment Motor 2.2~5kw | The devices are connected, and the power is equipped according to the length |