Chicken manure organic fertilizer production line is based on fresh chicken manure as raw material, after a series of processing, to produce natural organic chicken manure fertilizer complete sets of production equipment. The supporting equipment of chicken manure organic fertilizer needs fermentation and stacking machine, organic fertilizer crusher, horizontal mixer, granulator, rotary dryer, cooling machine, drum screening machine, envelope machine, packaging machine, conveyor and other equipment. Chicken manure organic fertilizer production line can be customized according to customer requirements, to provide 1-100 tons/hour of organic fertilizer production line, the output size is not the same price is different
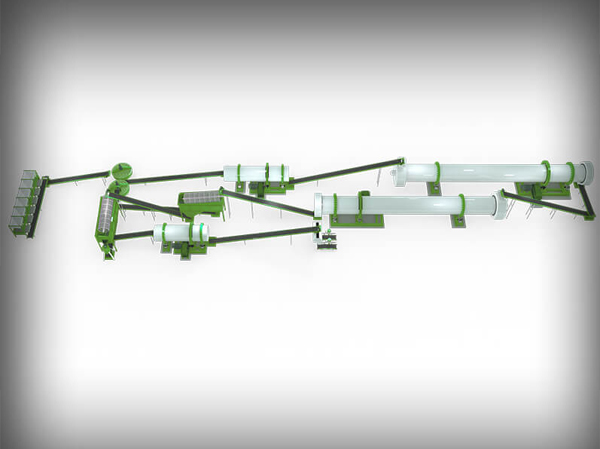
Automatic chicken manure fertilizer production line
processing capacity:1-100T/h
Application scope:poultry animal manure processing into fertilizer
Chicken manure processing machine is mainly used for turning chicken waste into organic fertilizer. If you have lots of chicken manure to handle or you want to begin a fertilizer manufacturing business, it is a good choice for you to buy a set of chicken manure making equipment. Chicken poo is good material for making organic fertilizer. With the chicken fertilizer production equipment, the process will be easier. What’s more, your compost period will be shorter, improving your production efficiency. Meanwhile, new designed organic fertilizer granulator machine has high granulation rate, bringing you more economic effects. Especially, there are different configurations of production equipment for your reference, you can choose a set of processing machine according to your plant requirements.

Chicken manure organic fertilizer production line process flow:
Environmental protection type chicken manure organic fertilizer equipment production line with chicken manure (straw, pig manure, cow manure) as the main raw materials through the trough turning machine — forklift bin — semi-wet material shredder — horizontal mixer — disk, new organic fertilizer granulator — organic fertilizer dryer — organic fertilizer cooling machine; Roller screening machine — organic fertilizer coating machine — automatic quantitative packaging scale.
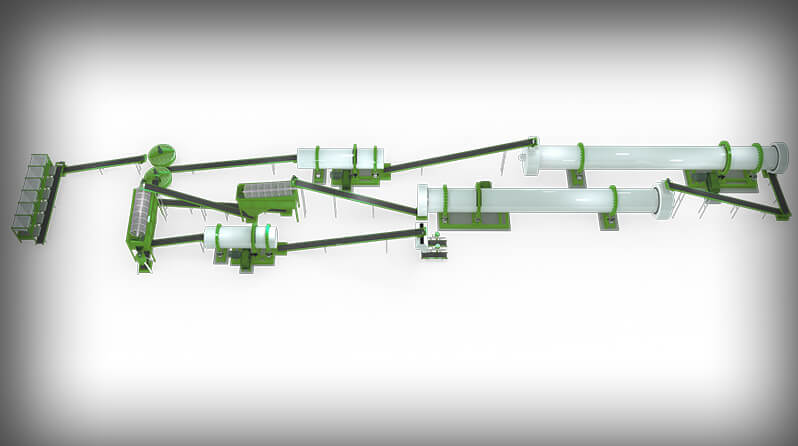
Chicken manure organic fertilizer production line system configuration:
Organic fertilizer production line equipment is mainly composed of fermentation system, drying system, deodorization and dust removal system, crushing system, batching system, mixing system, granulation system, screening system and finished product packaging system.
Granular organic fertilizer production line equipment: manure dewatering machine, fermentation pile turning machine, semi-wet material shredder, horizontal mixer, granulator, dryer, cooler, roller screening machine, envelope machine, packaging equipment, belt conveyor and so on.
Powder organic fertilizer production line equipment: fermentation pile turning machine, semi-wet material crusher, horizontal mixer, granulator, roller screening machine, packaging equipment, belt conveyor and so on.
Chicken manure organic fertilizer production line is based on chicken manure as raw material, through a full set of fertilizer production system processing, configuration plan can be based on customer’s production demand, selection, a variety of advanced production technology: disc granulation, gear granulation, powder organic fertilizer and other equipment program.
Chicken manure is a relatively high-quality organic fertilizer, which contains pure nitrogen, phosphorus (P2O5), potassium (K2O) about 1.63%, 1.54%, 0.085%. Chicken manure must be decomposed before application, and the parasites in chicken manure and their eggs, as well as some infectious bacteria can be inactivated and deodorized through the process of decomposition. Chicken manure organic fertilizer production process is closely related to the equipment configuration of organic fertilizer production line, general organic fertilizer production line equipment is mainly composed of fermentation system, drying system, deodorization and dust removal system, crushing system, batching system, mixing system, granulation system, screening system and finished product packaging system. The production process of chicken manure organic fertilizer roughly includes: raw material selection (chicken manure, etc.) → drying and sterilization → mixing of ingredients → granulation → cooling and screening → metering and sealing → storage of finished products.
The more complex chicken manure organic fertilizer production process is as follows: Organic fertilizer raw materials (animal manure, domestic waste, dead leaves, biogas residue, waste bacteria, etc.) after fermentation into the semi-wet material crusher for crushing, and then add nitrogen, phosphorus and potassium and other elements (pure nitrogen, phosphorus pentoxide, potassium chloride, ammonium chloride, etc.) to make the mineral elements to meet the required standards, and then have a blender to stir, and then enter the granulation mechanism particles, after drying, Through the screening machine, qualified products are packaged, and unqualified products are returned to the granulator for granulation.
Among them, the reasonable collocation of the fineness of raw materials is crucial to the production process of organic fertilizer. According to the experience of Tongda Heavy Industry, the fineness of the entire raw material should be matched as follows: 100-60 raw materials account for about 30%-40%, raw materials with a diameter of 1.00mm account for about 35%, and small particles with a diameter of 1.00-2.00mm account for about 25%-30%, the higher the fineness of the material, the better the viscosity, and the higher the surface finish of the particles after granation. However, in the production process, the use of excessive proportion of high fineness materials is prone to problems such as too large particles and irregular particles due to too good viscosity.
Chicken manure fertilizer production line configuration — raw material fermentation and crushing part
NAME | Specifications | Quantity | Remark |
---|---|---|---|
Trough tipping machine | ZCFD-3000 | 1 | Includes a shift car (tank changing car), shift motor, electrical control cabinet, remote control handle, and cable drum for customer selection (The track needs to be purchased by the customer) According to customer requirements, our company has flipping equipment with a width of 2-20 meters and a flipping depth of 0.8-3 meters. |
Forklift feeder | ZCW-2030 | 1 | Includes uniform discharge device, anti smashing net device, mixing anti blocking device, and vibration anti blocking device. The capacity of the silo is about 5m3, greatly reducing the workload of the forklift operator, and the forklift driver can also operate the stacker. The function of this device is to uniformly transport raw materials to the crusher. |
Drum screen | ZGS-1240 | 1 | The screen mesh is made of stainless steel material to prevent corrosion. According to customer requirements, a striking anti sticking net device can be added. |
Vertical composite mill | ZLFF-600 | 1 | The crusher adopts a chain blade composite structure, which can crush materials with a moisture content of less than 40% to a granulation state. The chain is made of high manganese alloy, and the blades are made of spring steel material, which has the advantage of durability and wear resistance. The rotor is dynamically balanced and can operate stably without the need for a foundation. |
Three warehouse dynamic batching | ZZP-1515 | 4 | The size of this silo is customized according to the customer’s ratio. The part in contact with the material can be made of 304 stainless steel material. The computer quantitative weighing system adopts imported sensors and instruments, with high measurement accuracy, ingredient accuracy of ≤± 0.5%, packaging accuracy of ≤± 0.2%, and reliable operation. |
Chicken manure feed production line configuration — granulation part
NAME | Specifications | Quantity | Remark |
---|---|---|---|
Single-shaft mixer | ZSJ-0830 | 1 | The mixing blade adopts a double spiral structure, which ensures uniform mixing and high efficiency. The mixing blades are made of high-strength and wear-resistant materials, which have a longer service life. The minimum gap between the rotor and the shell can be adjusted to near zero, effectively reducing the amount of material residue. Mixing capacity: 5-8t/h Body thickness: 6mm Dimensions: 3800 * 1320 * 770mm Reducer model: JZQ350-31.5 Mixing speed: 34r/min |
Stir tooth granulator | ZZGZ-600 | 1 | The interior of the barrel is lined with rubber sheets, which automatically remove scars. Anti corrosion insulation. The support wheel frame and transmission gear ring roller belt of the granulator are all made of cast steel material. Barrel thickness: 14mm, barrel inner diameter: 1800mm, barrel length: 6000mm. Material Q345. Adopting a one-time forming spiral tube. Production capacity: 7-9t/h Rotation speed: 11.5r/min |
Rotary dryer | ZHG-1010 | 1 | The dryer cylinder is a 14mm thick integrated spiral tube, which has the advantages of high concentricity, strong rigidity, and smooth operation. The thickness of the lifting plate is 8mm. The gear ring, rolling belt roller, and bracket are all cast steel parts. The induced draft fan is self-made by the company and has undergone static and dynamic balance calibration, resulting in stable and high-intensity operation. Adopting a co current drying method, the material and heat source airflow enter the drying equipment from the same side, resulting in a low outlet temperature and high thermal efficiency of the dryer. Choose reasonable operating parameters to balance the “coal, material, and air”, thereby greatly improving the thermal efficiency of the dryer and reducing drying energy consumption by more than 30-50%. |
Rotary cooling machine | ZLQ-0880 | 1 | The cooling machine cylinder is a 14mm thick integrated spiral tube, which has the advantages of high concentricity, strong rigidity, and smooth operation. The thickness of the lifting plate is 6mm. The gear ring, rolling belt roller, and bracket are all cast steel parts. The induced draft fan is self-made by the company and has undergone static and dynamic balance calibration, resulting in stable and high-intensity operation. Choose reasonable operating parameters to balance the “material and air”, thereby greatly improving the cooling efficiency of the cooling machine and reducing cooling energy consumption by more than 20-50%. |
Drum screen | ZGS-1240 | 1 | The screen mesh is made of stainless steel material to prevent corrosion. According to customer requirements, a striking anti sticking net device can be added. The function of this screening machine is to screen the crushed raw materials, the finished products enter the granulation process, and the waste products are returned for re crushing. The finished product is also a powdered organic fertilizer |
Chicken fertilizer feed production line configuration — supporting equipment
NAME | Specifications | Quantity | Remark |
---|---|---|---|
There is a bucket pellet packaging machine | ZKB | 1 | The parts in contact with the material are made of 304 stainless steel material. Specially designed feeding and bucket metering are carried out simultaneously with bagging and unloading. Save one-third of homework time, fast packaging speed, and high packaging accuracy. Imported sensors and pneumatic actuators are used, which are reliable in operation and easy to maintain. Measurement accuracy is plus or minus two thousandths. Wide quantitative range, high accuracy, combined with a conveyor sewing machine that can be raised and lowered on the table, making it versatile and efficient. |
Finished product warehouse | ZLC-1200 | 1 | The finished organic fertilizer warehouse is widely used in various fertilizer production lines to undertake the transfer equipment that is quickly transported to the belt conveyor and transported by the belt conveyor to the next deep processing link. This finished product warehouse, equipment material quality, durable. |
Chain return mill | ZLTF-500 | 1 | The outer wall of the crusher is made of 8mm thick manganese steel plate. The crusher chain adopts a high-strength alloy chain. The crushed material is uniform, not easy to stick to the wall, and easy to clean. The inner wall can be made of rubber or stainless steel (depending on customer needs) to achieve a smooth surface and easy cleaning. Quick opening maintenance doors are installed on both sides of the body, and the body and transmission device are mounted on a steel base. A shock absorber is installed at the bottom of the base and connected to the foundation. |
Cyclone dust collector | ZXC-900 | 2 | The cyclone dust collector has a simple structure, is easy to manufacture, install, and maintain, and has low equipment investment and operating costs. The cyclone dust collector is composed of an intake pipe, an exhaust pipe, a cylindrical body, a conical body, and an ash hopper. Each component of the cyclone dust collector has a certain size ratio, and the diameter of the dust collector, inlet size, and exhaust pipe diameter are all accurately calculated by engineers. Ensure the best dust removal effect is achieved. |
Induced draft fan | ZYF-6C | 15 | The induced draft fan is self-made by the company and has undergone static and dynamic balance calibration, resulting in stable and high-intensity operation. The induced draft fan and connecting pipeline are matched with the dryer. The impeller consists of 10 aft inclined blade types, a curved front plate, and a flat rear plate. Made of copper plate or cast aluminum alloy, and calibrated for dynamic and static balance, it has good air performance, high efficiency, and smooth operation. The air inlet is made as a whole and installed on the side of the fan. The cross-section parallel to the axial direction is curved, which allows gas to enter the impeller smoothly with minimal loss. |
The production process design of chicken manure organic fertilizer includes:
- Efficient composite bacterial strains and their propagation techniques;
- Advanced raw material blending technology and biological fermentation system;
- High quality fertilizer formula technology (can flexibly design product formulas based on local soil and crop characteristics);
- Reasonable secondary pollution (exhaust gas and gas) control technology;
- Design and manufacturing technology for complete sets of process equipment for fertilizer production.