Air separation equipment is to use air as raw material, through the compression cycle deep freezing method to turn air into liquid, and then through rectification and gradually separate from the liquid air to produce oxygen, nitrogen and argon and other inert gases equipment.
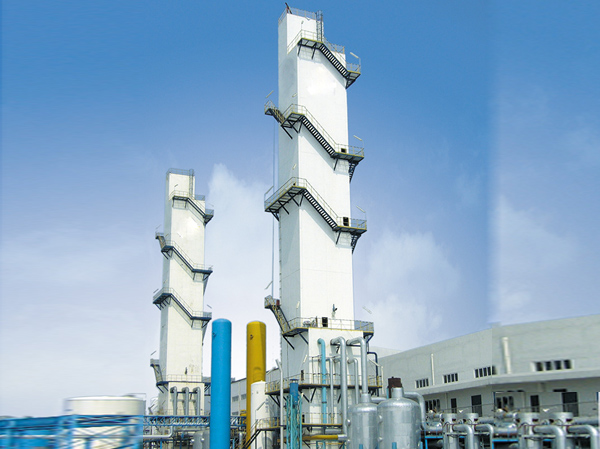
Air separation processing machine
There are many forms and types of air separation equipment. There are devices for the production of gaseous oxygen and nitrogen, and there are devices for the production of liquid oxygen and nitrogen. But as far as the basic process is concerned, there are four main types, namely, high pressure, medium pressure, high and low pressure and full low pressure process.
The production scale of air separation equipment has been able to produce only 20m3/h (oxygen) oxygen generators from the early days. It has developed the capacity to produce 20000 m3/h, 30000 m3/h, 50000 m3/h and 60000m3/h large air separation equipment, and has completed the scientific research stage, and will be able to manufacture 80000m3/h super large air separation equipment.
Purification principle of air separation equipment
In the oxygen production equipment using the principle of low temperature rectification, in order to ensure the normal operation of air distillation separation in the low temperature region, the air must be filtered, pre-cooled and purified in the normal temperature region.
Air contains a lot of dust, air turbine compressor (referred to as air compressor) in a long time of high-speed operation, dust will cause wear, corrosion and scaling of the impeller, blade and other parts of the machine, shorten the service life of the machine, so the raw material air filter must be set to remove dust in the air.
The air temperature after compressed by the air turbine compressor rises to more than 80 degrees, resulting in subsequent adsorption and heat transfer cannot be carried out normally. By setting an air precooling system, the air temperature entering the air separation equipment can be effectively reduced.
In addition to a large number of dust in the raw air, there are water, carbon dioxide, and acetylene and other hydrocarbons, most of the modern air separation equipment uses molecular sieve purification system to remove these impurities, in order to improve the cleanliness of the air into the cold box, to prevent water and carbon dioxide concentration and threaten the normal operation of the air separation equipment. Therefore, gas filtration, precooling and purification equipment is an indispensable part of the air separation equipment.
There are five kinds of dust removal mechanism:
1 Inertial impact: Smaller particles can pass through the micropores of the filter, but through the path of the filter medium, the particles have enough mass and momentum to collide with the filter fiber and be blocked and captured.
2 Brownian diffusion: Very small particles have very small mass, and when they are diffused with the Brownian motion of the air stream, they collide with the filter fiber and are filtered out.
3 Direct blocking: For particles of dust particles greater than 1 micron, when filtering the microhole of the medium material, the particle diameter is larger than the microhole diameter, and it is directly blocked and intercepted to achieve the purpose of removing impurities.
4 Gravity settlement: Dust particles are continuously collected until their mass becomes large enough to fall to the bottom of the filter under the action of gravity, or be discharged by the ash valve.
5 Electrostatic sedimentation: static electricity causes dust to change its movement trajectory and crash into obstacles, and electrostatic force participates in the work of sticking.
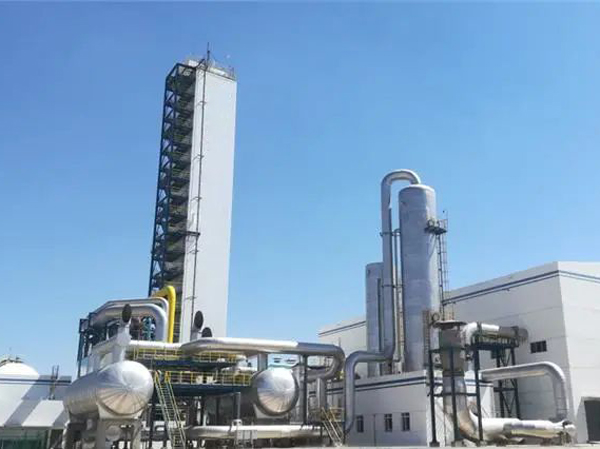
System composed of air separation equipment
Air separation equipment is a large complex system, mainly composed of the following subsystems: power system, purification system, refrigeration system, heat exchange system, distillation system, product delivery system, liquid storage system and control system.
Dynamic system
Mainly refers to the raw material air compressor. The air separation equipment separates the air by low temperature to obtain oxygen, nitrogen and other products, which is essentially completed by energy conversion. The energy of the device is mainly input by the raw air compressor. Accordingly, most of the total energy consumption required for air separation is the energy consumption of raw air compressors.
Purification system
It is composed of air precooling system (air cooling system) and molecular sieve purification system (purification system). The compressed raw material air temperature is high, and the air precooling system reduces the temperature of the air through contact heat transfer, and can wash the harmful impurities such as acidic substances. The molecular sieve purification system further removes water, carbon dioxide, acetylene, propylene, propane and nitrous oxide from the air, which are harmful to the operation of the air separation equipment.
Refrigeration system: The air separation equipment is cooled by expansion, and the refrigeration of the entire air separation equipment strictly follows the classic refrigeration cycle. However, the air separation refrigeration equipment usually mentioned mainly refers to: expansion machine.
Heat exchange system
The heat balance of the air separation equipment is accomplished through the refrigeration system and the heat exchange system. With the development of technology, the heat exchanger mainly uses aluminum plate fin heat exchanger.
Rectification system
The core of air separation equipment, the important equipment to achieve low temperature separation. High and low pressure two-stage distillation is usually adopted. It is mainly composed of low pressure tower, medium pressure tower and condensing evaporator.
Product delivery system
Oxygen and nitrogen produced by air separation equipment require a certain pressure to meet the use of subsequent systems. As long as it is composed of a variety of different specifications of oxygen and nitrogen compressors.
Liquid storage system
The air separation equipment can produce a certain amount of liquid oxygen and liquid nitrogen and other products to enter the liquid storage system for use when needed. As long as it is composed of a variety of different specifications of storage tanks, cryogenic liquid pumps and carburetors.
Control system
Large air separation equipment adopts computer distributed control system, which can realize automatic control.
Air separation equipment from the process can be divided into five basic systems:
Purification system for impurities
Mainly through air filters and molecular sieve absorbers and other devices to purify the air mixed with mechanical impurities, water, carbon dioxide, acetylene and so on.
Air cooling and liquefaction systems
It is mainly composed of air compressor, heat exchanger, expansion machine and air throttle valve, etc., which plays the role of deep freezing of air.
Air distillation system
The main components are distillation tower (upper tower, lower tower), condensation evaporator, subcooler, liquid air and liquid nitrogen throttle valve. It plays the role of separating various components in the air.
Heating and blowing system
The purification system is regenerated by heating and blowing.
Instrument control system
The whole process is controlled by various instruments.
Air separation equipment project case overview
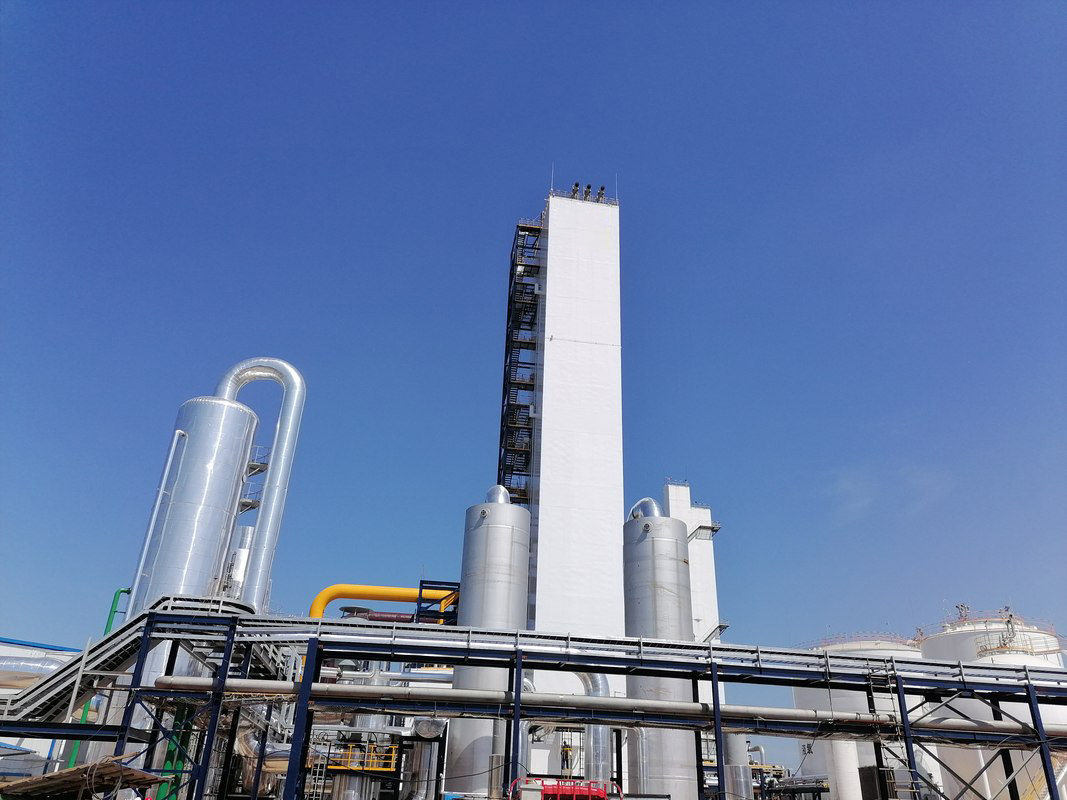
Project profile
300/350 air separation equipment for export to Australia.
Product advantage
Energy-saving technology
1, air compression system:
The discharge pressure of the air compressor is reduced from the traditional 0.52MPaG to 0.42MPaG
2, pre-cooling system:
The resistance of air cooling tower decreases from 10KPa to 6KPa
The use of the highest low resistance packing not only ensures the heat transfer performance of the tower, but also reduces the resistance
Liquid distribution device adopts new, state-of-the-art and advanced distributor to ensure the heat transfer performance of the tower under the premise of reducing the frozen water; High gas flux greatly reduces internal resistance.
Chiller adopts small flow and large temperature difference type; Chilled water pump flow reduced by more than half;
- Purification system:
The resistance of the adsorber decreases from 8KPa to 4KPa
The unit adsorption capacity was increased by 50% by using type III molecular sieve adsorbent. When the regeneration power is reduced, the resistance is also reduced
- Fractionating tower system
The lower tower, upper tower and argon tower adopt regular packing;
The filler is the new PLUS; Distillation efficiency increased by 20%
The plate heat exchanger adopts the new structure, and the resistance of the main heat exchanger is reduced from 15KPa to 10KPa
Using multi-layer main cooling, the heat transfer temperature difference can be reduced from 1.6K to less than 0.9K
- Control system
Flow measurement using bar flowmeter, resistance from 3-4KPa reduced to 0.5-1KPa
Comparison of energy consumption
Serial number | name | Design index | JB/T8693-2015 | Actual operation | The operation of other enterprises |
1 | Air compressor discharge pressure MPa | 0.42 | ——– | 0.42 | 0.52 |
2 | Air compressor flow Nm3/h | 58000 | ——– | 57225 | 61000 |
3 | Energy consumption per unit equivalent of oxygen production 0.42KW.h/m3 | 0.42 | 0.438 | 0.419 | 0.461 |
4 | Compared with the national standard energy consumption % | 95.9 | 105 |
Technical parameter
According to the site conditions specified by the user, the air separation device simultaneously produces several products to achieve the following quantity and quality:
Product name | yield Nm3/h | purity | Out-of-bounds pressure MPa(A) | Outbound zone temperature ℃ | remark |
Oxygen gas | 250 | ≥99.6%O2 | 0.12 | 40 | |
Nitrogen gas | 300 | ≤10PPm O2 | 0.11 | 40 |
Operating characteristic
- Operation cycle and device life
The continuous operation cycle of the unit is 2 years, except for simple maintenance.
Device design life ≥20 years.
In accordance with the instructions of Party B, the main equipment provided by Party B can meet the requirements of this Contract within 5 years.
- Running time
Under normal operation, the operation cycle from the time the unit needs to be fully thawed is 2 years.
- Driving time
After all thawing, the driving time to reach the designed product yield: about 36 hours.
Driving time to generate oxygen after temporary parking:
Oxygen is produced 4 to 6 hours after 8 hours of parking
Oxygen is produced 8 to 10 hours after 24 hours of parking
4, the time required to discharge the liquid from the cold box (tower and condenser) : about 8 hours
- The time required for thawing in the cold box (without argon production system) : about 36 hours
Operating elasticity
The oxygen producing device can operate in the range of 75%~105% of the designed oxygen output under variable load conditions without any additional equipment (under the design conditions), and meet the requirements of larger and smaller quantities of products.
Air separation equipment supporting unit
Matching unit | quantity |
Air filtration compression system | 2 Set |
Precooling system | 1 Set |
Purification system | 1 Set |
Fractionating system | 1 Set |
Turbocharger expansion unit | 2 Set |
Liquid storage and vaporization system | 1 Set |
Oxygen pressure system | 1 Set |
Nitrogen pressure system | 1 Set |
Gas storage and pressure regulation system | 1 Set |
Electronic control system | 1 Set |
Instrument control system | 1 Set |
What are the application fields of air separation equipment
the application of air separation equipment in the field of petrochemical
Air separation equipment has been widely used in the field of petrochemical, the most common is to separate air into oxygen, nitrogen and other gases, in order to be used in the petrochemical production of welding, cutting, spraying, heat treatment and other processes. In addition, air separation equipment can also be used in petrochemical production degassing, hydrogen preparation and other links.
the application of air separation equipment in the field of metallurgy
The metallurgical industry is also one of the important application areas of air separation equipment, which is often used in the smelting and production process of iron, steel, copper and other metal materials. In the smelting equipment such as blast furnace and converter, due to the need to reduce and melt the ore from the heat generated by the combustion of ore and coke, a large amount of oxygen is required. At this time, the air separation equipment plays an important role in the preparation of oxygen.
the application of air separation equipment in the field of medicine
The application of air separation equipment in the pharmaceutical industry is mainly to prepare oxygen in the air into oxygen gas, which is used for oxygen therapy, rescue and other treatment means. In emergency vehicles, hospitals and other places, some patients need to breathe through a respirator, which requires high purity oxygen. At this time, air separation equipment is widely used in the field of medicine.
In summary, as a kind of equipment for physical or chemical absorption and separation of mixed gases, air separation equipment has a wide range of applications in petrochemical, metallurgy, medicine and other fields.