The main steps of the waste tire and plastic refining production line include feeding, heating, non condensable gas treatment, smoke and dust treatment, slag removal, carbon black, steel wire removal, and tire oil
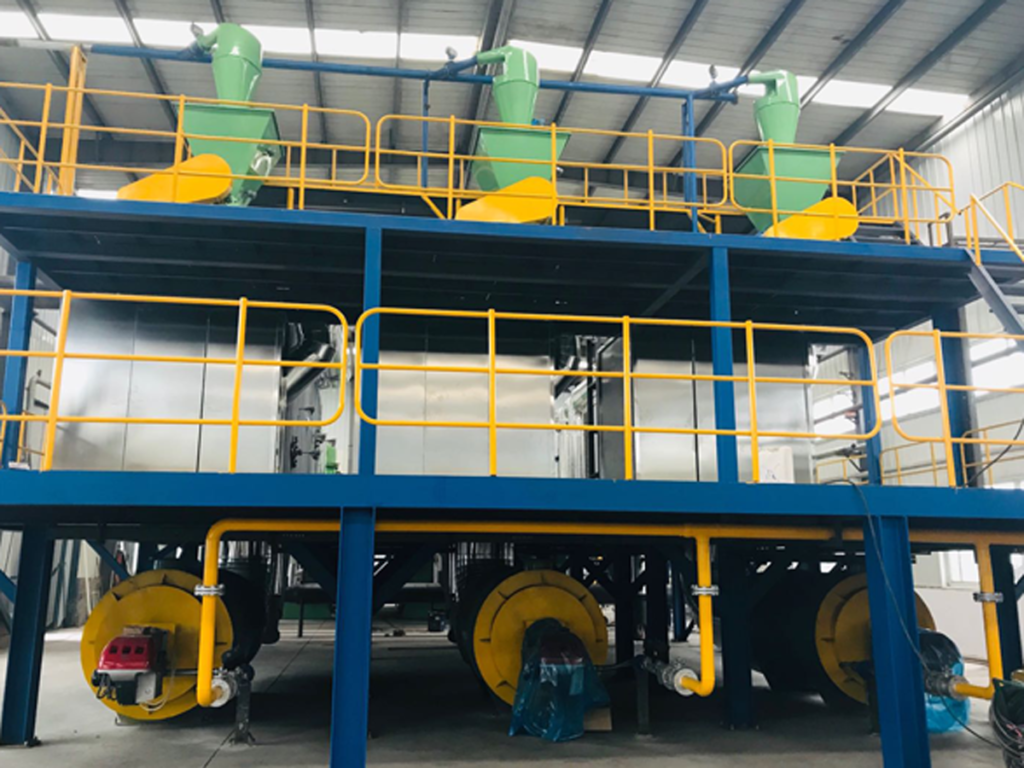
Process of Refining Production Line for Waste Tires
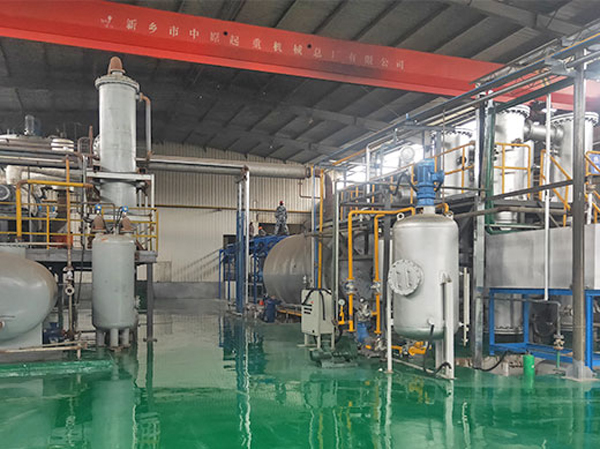
Process of Refining Production Line for Waste Tires
Feeding – Waste tires are fed into the reaction vessel through an automatic feeder.
Step 2: Heating – The reaction kettle can be uniformly heated using cracked oil or natural gas. When heated to about 260 degrees, the cracked oil and gas enter the cooling system and liquefy into oil, which then enters the intermediate oil tank.
Step 3: Non condensable gas treatment – Gas that cannot be liquefied at room temperature and pressure will be fully burned by the combustion machine at the bottom of the furnace, which is energy-saving and environmentally friendly.
Step 4: Smoke and dust treatment – All smoke and dust generated by combustion are treated in a professional industrial gas purification device to ensure that the final emissions meet the standards.
Step 5: Slag Removal (Carbon Black) – The automatically discharged slag is transported to the slag storage bin through pipelines by negative pressure air conveying equipment to ensure that the slag removal process is dust-free.
Step 6: Remove the steel wire – When removing the steel wire, cooperate with the ventilation and dust removal equipment to ensure that there is no dust
The process flow of waste tire refining equipment mainly includes the following steps:
Feed: Waste tires are fed into the reaction vessel through an automatic feeder, ensuring that the furnace door is tightly closed and creating a closed high-temperature environment. This step can be completed manually or through a hydraulic automatic feeding system.
Heating: Use cracked oil or natural gas to uniformly heat the reaction kettle. When heated to about 260 degrees, the cracked oil and gas enter the cooling system and liquefy into oil, which then enters the intermediate oil tank.
Non condensable gas treatment: Gas that cannot be liquefied at room temperature and pressure will be fully burned by the combustion machine at the bottom of the furnace, achieving energy conservation and environmental protection.
Smoke and dust treatment: All smoke and dust generated by combustion are treated in a professional industrial gas purification device to ensure that the final emissions meet the standards.
Slag discharge (carbon black): The automatically discharged slag is transported to the slag storage bin through pipelines by negative pressure air conveying equipment, ensuring that the slag discharge process is dust-free.
Wire out: When wire out, cooperate with exhaust and dust removal equipment to ensure no dust.
The entire process of refining waste tires has been automated, efficient, and environmentally friendly, equipped with advanced control systems and safety devices to ensure easy operation, safety, and reliability. At the same time, the high oil yield and resource recycling characteristics make this technology have high economic value and environmental significance.
In addition, the refining process also involves pre-treatment stages, including removing steel wires, cutting tires, magnetic screening, and other steps to ensure the efficiency and safety of the refining process. The entire process pays attention to environmental protection and resource recovery. Through professional industrial gas purification equipment, smoke and dust are treated to ensure standard emissions. At the same time, non condensable gas and carbon black are recycled and reused to achieve maximum resource utilization and environmental protection
How many large factories are needed to open a tire refinery
The land area occupied by waste tire refining equipment varies depending on its scale and operating mode. Intermittent waste tire refining equipment ranging from 1-15 tons, occupying an area of approximately 450 to 600 square meters; The fully continuous waste tire refining equipment with a processing capacity of 50 tons requires approximately 1200 square meters of space. For large-scale operations, such as the annual processing of 20000 tons of waste tire refining projects, the land area of the cracking workshop itself may be expanded to 1500 square meters, plus storage, oil tank areas, and necessary safety buffer zones, the total area is estimated to be between 2000 and 3000 square meters.
Regarding the overall layout planning of the tire refinery, several core suggestions are as follows:
Regulatory compliance: Ensure that the design scheme fully complies with relevant national laws and regulations on fire safety, public health, good ventilation, sufficient sunlight, and environmental protection.
Scientific zoning: Optimize the layout of various functional areas, including raw material warehouses, production lines, finished product warehouses, office areas, etc., to promote efficient logistics flow and convenient daily management.
- Safety interval: Based on safety considerations, appropriate spacing should be set between the cracking workshop and adjacent buildings to reduce potential risks.
Environmental protection facilities: equip necessary environmental protection facilities to ensure that emissions such as exhaust gas and wastewater meet emission standards after treatment.
Logistics optimization: Carefully plan logistics routes to prevent cross contamination, facilitate the entry and exit of raw materials and product transportation.
Future development: Reserve expansion space during design to meet the growth needs of the enterprise in the future.
At the same time, the planning also needs to fully consider the local climate, geological conditions, and surrounding environmental factors, and rely on our professional engineering team for in-depth design
What is the profit margin of tire refining
The profit of tire refining is considerable, and the specific profit size is influenced by various factors. Below are examples of calculating the prices of waste tires and tire oil in China. Please calculate based on local conditions
Refining waste tires is an investment with high profit potential. According to market conditions, the market price per ton of waste tires is between 2800-3000 yuan, with carbon black and steel wire values of 300-450 yuan and 1000-1200 yuan, respectively. Even according to the lowest calculation standards, the profit per ton of waste tire extraction is close to 500 yuan, making waste tire extraction an attractive investment.
The technology of refining waste tires can produce tire oil, and this year’s tire oil price is about 5000 yuan/ton, while the price of waste tires is also around 2000 yuan/ton. On average, 2.5 tons of waste tires can be used to extract 1 ton of oil, while also producing about 0.8 tons of carbon black and 0.3 tons of steel wire. Considering the value of the produced tire oil and by-products, the gross profit of 2.5 tons of waste tires is approximately 1540 yuan. Generally speaking, waste tire refining equipment can process 10 or 15 tons of tires per day. Taking 10 tons as an example, the daily gross profit is about 6160 yuan.
The profit margin of tire refining is approximately maintained between 40% and 45%. By extracting 10 tons of waste tires, approximately 4 tons of tire oil can be produced, and additional products such as steel wire can also be obtained simultaneously. According to the current market price, the cost per ton of waste tires is about 1000 yuan, while the selling price of tire oil is as high as about 3000 yuan per ton. From this, it can be seen that there is indeed a considerable profit margin in extracting tire oil from waste tires.
In summary, the profit of tire refining is influenced by various factors such as market prices, raw material prices, supply, and market demand, so the actual profit may vary. Investors need to carefully evaluate market conditions and risks when considering investing in tire refining projects to ensure substantial profits