- Pyrolysis Refining Oil Plant
- 30tons per day
- Tire Plastic Oil
- In Vietnam
The conventional resource utilization direction of waste tire is the waste tire pyrolysis to liquid fuel, pyrolysis carbon black and waste steel wire recovery. Waste tire oil refining continuous pyrolysis production line, including raw material preheating system, reactor pyrolysis system, oil and gas cooling system, slag discharge and separation system, heating system, automation system, etc.
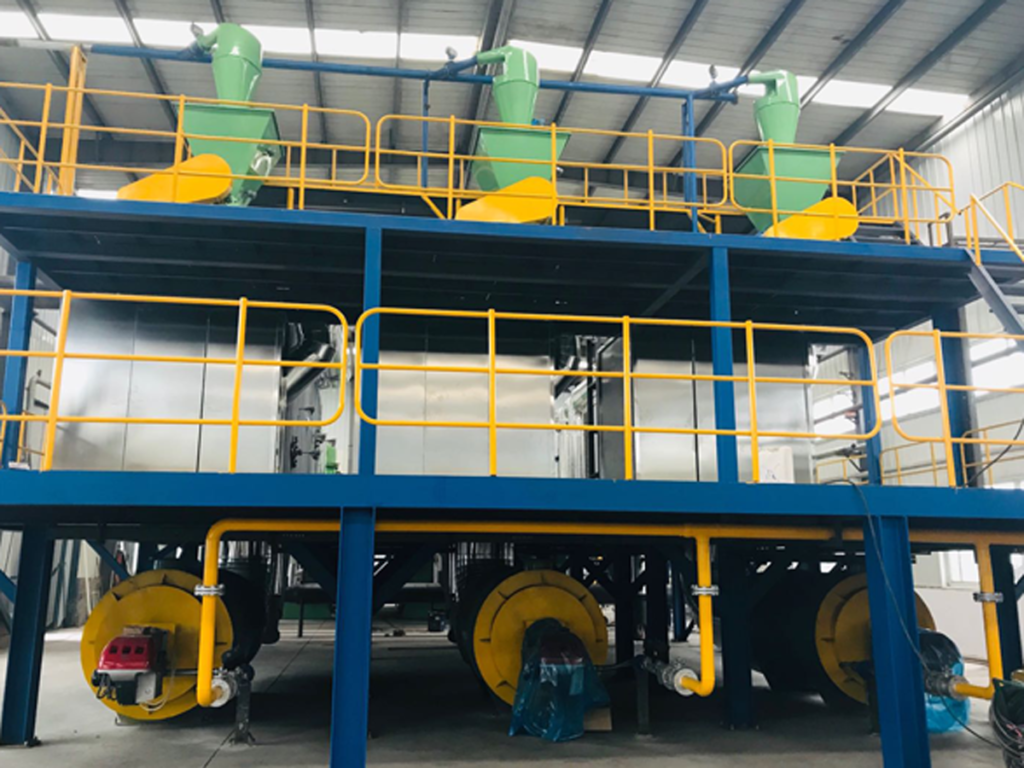
30tons per day Waste Tire Plastic Pyrolysis Refining Oil Plant In Vietnam
brief introduction of production device:
This production unit is a production line of diesel oil and by-products by using tire oil. It is mainly equipped with 1 × 2 × 2 sets of pretreatment reaction tank and horizontal rotary heating furnace, atmospheric fractionator, vacuum fractionator, tubular condenser, cooling water tank, oil-water separator, filter, refined filter tank, pretreatment system, heating system, distillation system, condensation system, vacuum negative pressure and waste. The system is composed of gas recovery treatment and utilization system, smoke and dust removal system, safety fire protection and explosion-proof electrostatic grounding system, water treatment and recycling system, automatic semi-automatic control system, etc.
The device adopts horizontal rotary heating furnace for heating, which can continuously produce and process capacity; 20-30t / D processing tire oil to produce diesel oil and by-products. (intermittent production line can be customized according to customer demand)
Process description
Step 1: loading: use a small grab to put the waste tires in the hopper of the hydraulic feeder, and automatically enter the reactor through the automatic hydraulic feeder, and close the loading door after loading.
Step 2: heating: use tyre oil or non condensable gas (the extra non condensable gas produced in the cracking process of several other equipment) to heat the reactor evenly. After heating for about 2 hours, the temperature gradually rises to about 260 ℃, and the cracked oil gas enters the cold system through the oil outlet in the reactor center and liquefies into oil into the intermediate tank.
Step 3: non condensable gas treatment: the non condensable gas (C1-C4 component) that flows into the oil tank together with the oil flows into the furnace after passing through two water seal fire arrestor devices and one fire arrestor device. This part of non condensable gas can be fully burned through the combustion machine, and a large part of fuel can be saved at the same time.
Step 4: smoke and dust treatment: all the smoke and dust generated by combustion are pumped into the general dust removal system by the special induced draft fan for treatment. The treated smoke and dust are white water vapor without black particles. Then the water vapor will enter the professional industrial purification device for standard emission treatment to ensure that the final smoke and dust emission meets the national emission standards.
Step 5: slag (carbon black) — after the reaction kettle temperature drops to the safety temperature, connect the automatic slag extractor to start slag discharging, and the discharged slag will be transported to the slag storage bin by the negative pressure air delivery equipment through the pipeline to ensure that the slag discharging process is dust-free.
Step 6: steel wire discharging: open the feeding door and use the automatic steel wire discharging machine to discharge the steel wire. When discharging the steel wire, cooperate with the suction and dust removal equipment to ensure no dust.